Gängige Fehler Planung beim Betrieb einer Gaswarnanlage
Aus den Erfahrungen seit 2008, mit vielen hunderten Projekten in nahezu allen Branchen, läßt sich feststellen, dass der Fehler seinen Ursprung in der Mehrheit der Fälle bereits bei der Planung einer Gaswarnanlage hat.
Dazu kommt, dass viele Betreiber das Thema der Dokumentation und Unterlagen so gar nicht ernst nehmen. Spätestens bei einem Vorkommnis wird alles genaustens geprüft und genau dann ist es zu spät sich diesem Thema anzunehmen. Dies bedeutet in fast allen Fällen eine Mitschuld für den Betreiber.
Und was sich auch feststellen läßt ist, dass die Größe einer Firma damit nichts zu tun hat. Viele große Firmen, haben oftmals mehr Defizite wie vergleichbare kleine Firmen der gleichen Branche.
Hier folgend eine Auflistung der häufigsten vorgefundenen Fehler unserer Projekte:
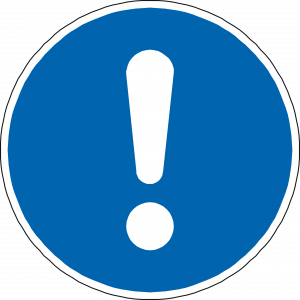
- Vertauschte Gasart: z. B. CO mit CO2
- Bei Explosionsschutz-Überwachung, Arbeitsplatzsicherheitsüberwachung fehlt
- TRGS 910 wird nicht beachtet bzw. überwacht
- Messstellen auf falsche Höhe platziert
- Falsche Position der Messstellen
- Keine Sicherheitsakte für die Messstellenposition
- Querempfindlichkeiten nicht beachtet
- Vergiftungen nicht beachtet
- Filter nicht kontrolliert
- Luftströmung nicht beachtet
- Zu wenige Messstellen (zu viele Messstellen ist nicht gefährlich, aber teuer)
- Falsches Messprinzip des Sensors
- Falscher Messbereich des Sensors
- Falsche Art der Messstelle, also z. B. Diffusion statt Absaugung
- Fehlendes Alarmierungskonzept
- Fehlende Gefährdungsbeurteilung
- Fehlendes Explosionsschutzkonzept
- Falsche Ex-Ausführung also z. B. 3G statt 2G
- Fehlende Baumusterprüfung der Messstellen
- Keine messtechnische Funktionsprüfung
- Keine Eignungsprüfung für verlängerten Wartungszyklus
- Fehlende Ex-Zulassung der Auswerteeinheit
- Einsatz von Produkte ohne Prüfung nach aktuellen Normen z. B. EN IEC 62990
- Fehlende Ausführung/Auslegung nach DIN EN Norm
- Einsatz in einer Branche mit DIN EN Norm-Vorgaben, ohne dafür geeignet zu sein
- Fehlende Wartung
- Wartungszyklus zu groß
- Unvollständige bzw. unzureichende Wartung
- Unvollständige Serviceberichte
- Fehlende jährliche Unterweisung der Mitarbeiter
- Fehlende Sichtkontrollen mit Dokumentation
- Unvollständige Unterlagen
- Einsatz von Firmen, welche vom Hersteller nicht autorisiert sind bzw. nicht über das Know-How für die Anlage (z. B. Zugriffscodes) verfügen
- usw.
Zusammenfassend läßt sich feststellen, dass viele Betreiber sich in falscher Sicherheit wiegen, nur weil diese eine oder mehrere Gaswarnanlagen im Einsatz haben.
Wenn auch nur einmal eine ausreichende Kontrolle aller Unterlagen, aktuellen Anforderungen und Inhalte der Unterlagen überprüft würden, dann würden sicher viele Probleme, Abweichungen und Notwendigkeiten direkt auffallen.
Es ist teilweise schon extrem gefährlich und erschreckend was in der Praxis, trotz diverser Vorgaben, alles an unbeachteten Risiken und Fehlern vorhanden ist, selbst bei den größten Firmen mit festen zuständigen Personen für die Gaswarntechnik.
Für die Menge an Fehlern und auch Gewichtigkeit selbiger, passiert extrem wenig. Jedoch ist jeder Unfall einer zu viel, genauso wie die Langzeitfolgen z. B. durch krebserregende Stoffe, welche oftmals gar nicht genügend beachtet werden.
Im nun Folgenden finden Sie ein paar Berichte über tatsächlich vorgefundene Tatsachen für den Bereich der stationären Gaswarntechnik. Aufgrund des Trends zur Verschwiegenheitserklärung ist es uns leider kaum noch möglich mehr Beispiele hier darzustellen. Aber wir versuchen diese zu ergänzen, soweit uns dies möglich ist.
Vorgefundene Szenarien aus der stationären Gaswarnbranche
Beispiel 1: Gaswarnanlage in gewerblich genutztem Mehrparteienhaus
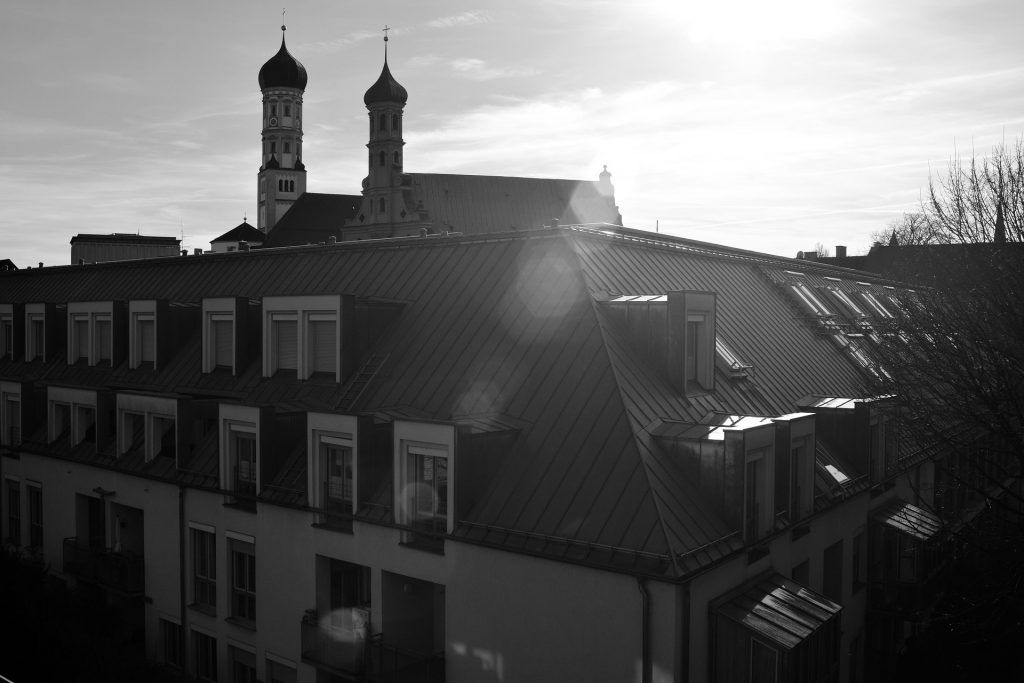
Ein Projekt im Ruhrgebiet. Dort sollen an sechs Messpunkten an der Außenwand (draußen) drei toxische Gasarten überwacht werden, aufgrund einer Auflage des Regierungspäsidiums. Dazu wurde eine Vorgabe von einem Prüfinstitut erstellt. Auf Grundlage dieser Vorgabe wurden Angebote von großen Herstellern und Händlern eingeholt. Die Spanne ging von 50.000,- bis 150.000,- Euro.
Vorweg sei bemerkt, dass keines der Angebote den Vorgaben des Prüfinstitutes entsprach.
Für wen entscheidet man sich nun?
Es wurde sich für den günstigsten Anbieter, eines Gaswarngeräte-Händlers, entschieden. Die Anlage wurde montiert und das Gebäude ging in Betrieb.
Nur wenige Monate vergingen und es gab die ersten Fehlalarme. Dies passierte immer wieder und führte zu entsprechenden teuren Feuerwehreinsätzen.
Nun reklamierte der Betreiber dies beim Gaswarngeräte-Händler. Dieser erklärte ihm, dass zum einen ein kurzer Wartungszyklus erforderlich ist und zum anderen die Sensoren regelmäßig einmal pro Jahr ausgetauscht werden müssen.
Und es kam noch besser.
Als dann tatsächlich einmal ein Störfall vorlag und eine Gaskonzentration auftrat, da reagierte die Gaswarnanlage nicht, weil der Wind dafür sorgte, dass die Luft nicht an die Sensorik gelangte, obwohl sich die Konzentration in der Nähe befand. Sicherlich verzögernd dürfte sich dabei auch das jeweilige Wetterschutzgehäuse bemerkbar gemacht haben.
Und…
Man hatte in der Zwischenzeit fast soviel an Folgekosten durch den jährlichen Sensortausch von 30 Sensoren usw. ausgegeben, wie die Differenz zu den hochpreisigeren Angeboten betrug.
Wie ging es aus?
Die Gaswarnanlage musste komplett demontiert werden, was natürlich auch seine Spuren am neuen Gebäude bzw. der Fassade hinterließ. Dann wurde ein neues absaugendes System eingebaut, welches die Luft an kleinen, kaum sichtbaren, Stellen ansaugte, diese filterte, die Feuchtigkeit entfernte, um dann unter gleichbleibenden klimatischen Bedingungen an den Sensor zu gelangen.
Dieses System hatte dann keine Fehlalarme, die Sensoren hatten eine normale Haltbarkeit und durch die Ansaugung wurde auch zuverlässig das Gas-Luft-Gemisch zum Sensor geführt.
Der Betreiber hingegen blieb auf seinen Kosten komplett sitzen und hat somit die erste Gaswarnanlage nebst Demontage, Feuerwehreinsätzen und teueren Sensorkosten an Lehrgeld aufbringen müssen, was man bei einer fachlichen Planung und Kontrolle der Angebote hätte vermeiden können.
Wie gut, dass niemand zu Schaden gekommen ist, aber die Schadenshöhe dürfte sicherlich bei rund 150.000,- Euro liegen.
Ursachen:
- Angebote wurden nicht fachlich geprüft
- Es wurde der günstigste Anbieter beauftragt
- Die falschen Produkte wurden eingesetzt
Verbesserungsvorschlag:
- Auslegung der Gaswarnanlage durch einen herstellerunabhängigen Fachkundigen
- Fachlich korrekte Ausschreibungstexte oder Lasten-/Pflichtenhefte
- Angebote fachlich prüfen, vergleichen und auswerten lassen
- Prüfung der Ausführung inkl. Unterlagen und Zulassungen
Beispiel 2: Gaswarnanlagen in Tiefgaragen nach VDI 2053 & DIN EN 50545
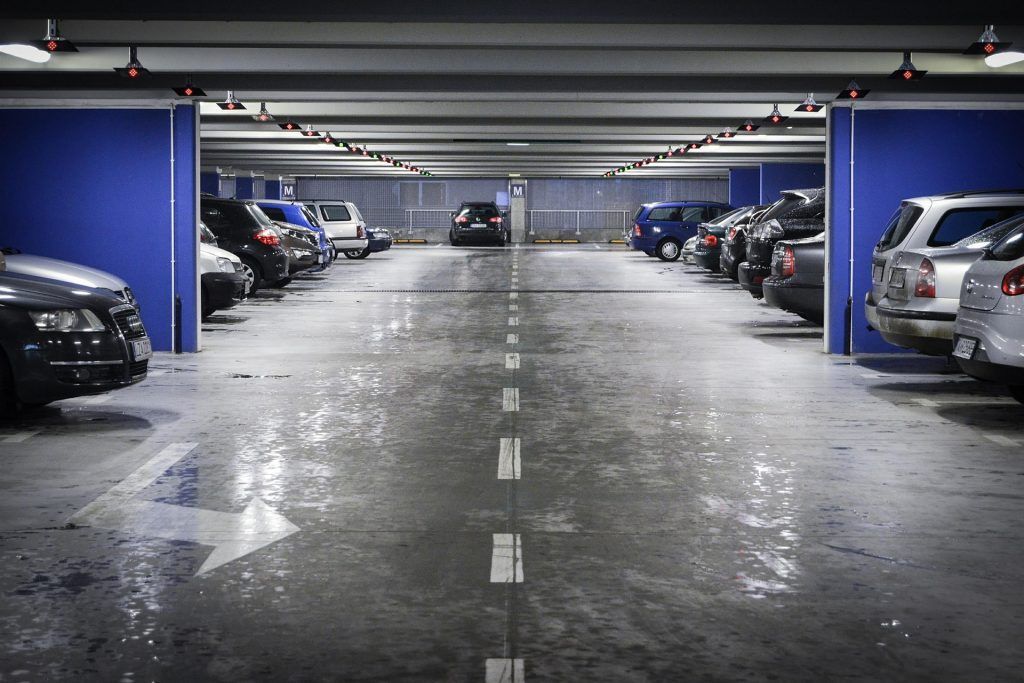
Es besteht eine DIN EN-Norm und Regelwerke bzw. Verordnungen, wie eine Gaswarnanlage auszuführen ist. Nun holte man sich Angebote ein und entschied sich für den günstigsten Anbieter. Die Gaswarnanlage wurde verbaut und in Betrieb genommen. Es ging jahrelang alles gut. Auf einmal reagierte die Gaswarnanlage nicht, als sie hätte reagieren müssen. Der Vorgang wurde von Extern geprüft und festgestellt, dass die Gaswarnanlage nicht nach den Regelwerken bzw. Verordnungen ausgeführt war, trotz Abnahme durch ein Prüfinstitut. Nun prüfte man die Zulassungen und stellte fest, dass dieses Produkt gar nicht die notwendige Zulassung hatte. Die ganze Tiefgarage wurde stillgelegt. Die Gaswarnanlage wurde ausgetauscht. Auch die komplette Kabelinstallation musste mit ausgetauscht werden. Der Vorgang dauerte drei Monate.
Ergebnis: Drei Monate stillgelegte Tiefgarage mit allen Unkosten plus die Kosten für eine komplett neue Gaswarnanlage inkl. Express-Zuschlag.
Ursachen:
- Fehlende Prüfung der Angebote
- Fehlende Prüfung der Ausführung
- Fehlende Prüfung der Produkte/Zulassungen
Verbesserungsvorschlag:
- Fachlich korrekte Ausschreibungstexte oder Lasten-/Pflichtenhefte
- Angebote fachlich prüfen, vergleichen und auswerten lassen
- Prüfung der Ausführung inkl. Unterlagen und Zulassungen
Hinweis dazu: Stand 2023 ist uns nur ein Hersteller (Oppermann Regelgeräte) bekannt, welche bis heute noch eine aktuelle Baumusterprüfung nach EN 50545 besitzen. Zusätzlich sind uns zwei weitere Hersteller bekannt, welche eine ausgelaufene Prüfbescheinigung haben.
Alle anderen deutschen Anbieter am Markt besitzen Stand 2023 keine gemäß der EN 50545 seit 2012 vorgegebene Baumusterprüfung zum Einsatz in Tiefgaragen und Tunneln.
Der Tiefgaragen-Betreiber welcher Hersteller ohne diese Baumusterprüfung einsetzt dürfte sich im Schadensfall mit dem Begriff „Grobfahrlässigkeit“ beschäftigen dürfen, was unter Umständen versicherungstechnisch nicht abgedeckt ist.
Und ein Tipp am Ende des Beispiels: Glauben Sie nicht alles was Ihnen ein Lieferant erzählt. Lassen Sie es sich schriftlich nachweisen und vergleichen Sie die Produktdaten des etwaigen Zertifikats. Und beachten Sie auch, dass eine Konformitätserklärung kein Baumusterprüfzertifikat ist.
Einen Beitrag dazu finden Sie hier.
Beispiel 3: Explosionsschutz
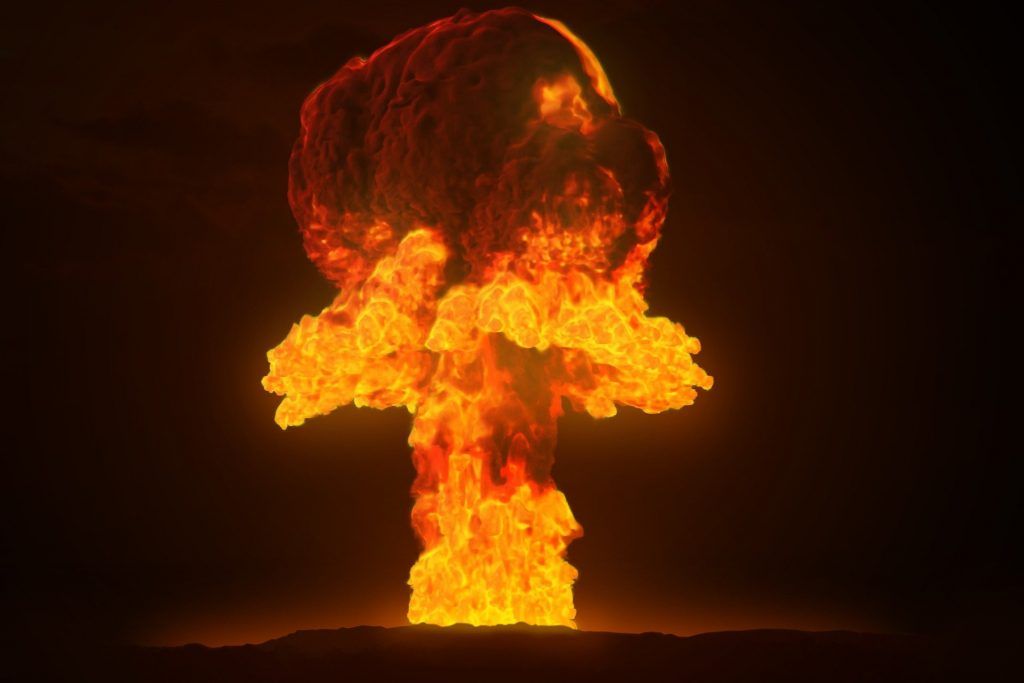
In einer Gefährdungsbeurteilung und einem Explosionsschutz-Dokument wurde eine Gaswarnanlage aufgeführt. Auf Grundlage dieser Unterlagen wurden Angebote eingeholt, verschiedene Firmen waren dazu vor Ort. Man entschied sich für einen Anbieter der mittleren Preisklasse, da dieser in der Nähe war. Die Gaswarnanlage bzw. Messstellen wurde in der Ex-Zone 1 montiert. Die Messstellen waren druckgekapselt und zugelassen für die Ex-Zone 1. Die Anlage ging in Betrieb. Nach einer Explosion prüfte die Staatsanwaltschaft den Fall und es kam heraus, dass zwar die Messstellen in Ordnung waren, aber die Auswerteeinheit selbst keine Zulassung bzw. Prüfung für die Ex-Zone 1, also 2G, besaß. Hinzu kam, dass die Messstellen über keine messtechnische Funktionsprüfung verfügten, so wie es gefordert war. Da der Hersteller die notwendigen Produkte nicht im Programm hatte, musste die ganze Gaswarnanlage inkl. Kabel demontiert und gegen eine Neue ersetzt werden. Die Kosten gingen in die Hunderttausende.
Der Kunde blieb auf dem Schaden sitzen (ausgenommen den Explosionsschaden).
Ursachen:
- Fehlende fachliche Prüfung der Angebote im Hinblick auf die erforderlichen Zulassungen
- Fehlende fachliche Prüfung vor der Inbetriebnahme inkl. Unterlagen und Zulassungen
Verbesserungsvorschlag:
- Auslegung der Gaswarnanlage durch einen herstellerunabhängigen Fachkundigen
- Fachlich korrekte Ausschreibungstexte oder Lasten-/Pflichtenhefte
- Angebote fachlich prüfen, vergleichen und auswerten lassen
- Prüfung der Ausführung inkl. Unterlagen und Zulassungen
Beispiel 4: Kältemittel-Gaswarnanlagen in Kühlräumen nach DIN EN 378
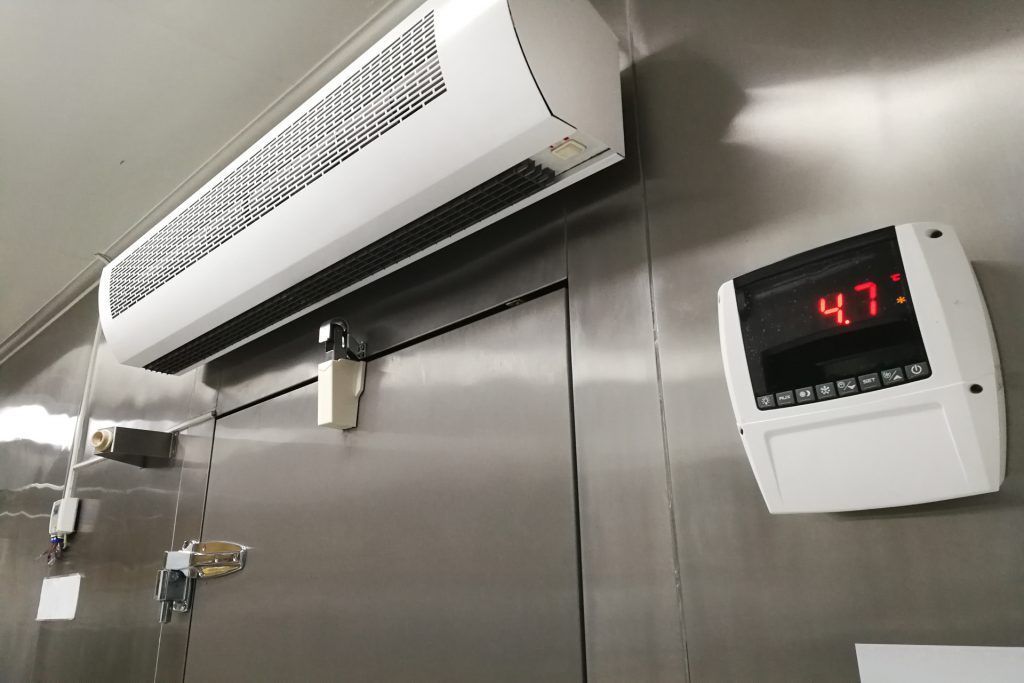
Ein großer Kühlraum in einem größeren Lebensmittel-Markt. In der Kälteanlage wurde das Kältemittel CO2 eingesetzt. Dies ist ein schweres Gas, welches zu Boden sinkt und sich ähnlich wie Wasser am Boden „bewegt“ und je nach Menge langsam „vollläuft”.
In diesem Raum wurden vier Messstellen für CO2 vorgesehen. Der Raum wurde regelmäßig durch ausspritzen mit einem Hochdruckreiniger gesäubert. Eines Tages ging ein Mitarbeiter in den Raum um etwas zu holen, wurde direkt ohnmächtig und fiel nach vorne in den Raum. Dies bekam ein zweiter Mitarbeiter mit, zog den Kollegen sofort aus dem Raum. Auch er wurde ohnmächtig und fiel nach hinten. Er hatte seinen Kollegen aber schon so weit nach hinten gezogen, dass dieser nicht mehr im Raum lag. Der dritte Kollege hat geistesgegenwertig die Tür geschlossen und die Feuerwehr gerufen.
Alle Mitarbeiter haben sich mit sehr viel Glück davon erholt. Es kam zu dem Vorfall, weil eine Leckage an einer Kältemittelleitung vorlag und CO2 in den Raum strömte. Der Raum war bis ca. 1,80 hoch mit CO2 vollgelaufen. Es reagierte keiner der Messstellen, weil man bei der Planung und Umsetzung den Begriff CO2 mit CO verwechselt hat. Man platzierte die Messstellen somit unterhalb der Decke. Diese hätten also erst reagiert, wenn der Raum bis zur Decke vollgelaufen wäre. Das war aber noch nicht alles. Weil der Raum mit dem Hochdruckreiniger gesäubert wurde, hat man die Messstellen in einen Kabelkanal gesetzt. Das Reinigungspersonal sollte dann bei der Reinigung den Deckel draufsetzen und danach wieder abnehmen. Der Deckel wurde jedoch seit jeher nicht wieder aufgemacht. Wer ist nun daran schuld, dass beinahe Menschen gestorben wären? Gute Frage.
Am Ende des Tages wäre es der Betreiber, also der Lebensmittelhändler. Wobei hier alle versagt haben. Der Planer, die ausführende Firma, die wartende Firma und der Betreiber.
Man hat es gut geschafft, dass dieser Vorfall nicht in die Medien kam. Leider gibt es zahlreiche solcher Vorfälle.
Ursachen:
- Unzureichende Planung im Bezug auf Besonderheiten
- Falsche Umsetzung bei der Platzierung von Messstellen
- Fehlende Abnahme bzw. Prüfung bei Inbetriebnahme
- Unzureichende Wartung und Kontrolle
Verbesserungsvorschlag:
- Auslegung der Gaswarnanlage durch einen herstellerunabhängigen Fachkundigen
- Fachlich korrekte Ausschreibungstexte oder Lasten-/Pflichtenhefte
- Angebote fachlich prüfen, vergleichen und auswerten lassen
- Prüfung der Ausführung inkl. Unterlagen und Zulassungen
- Wiederkehrende Prüfung der Unterlagen, besonders der Serviceberichte
Beispiel 5: Mobile Stickstoffbehälter
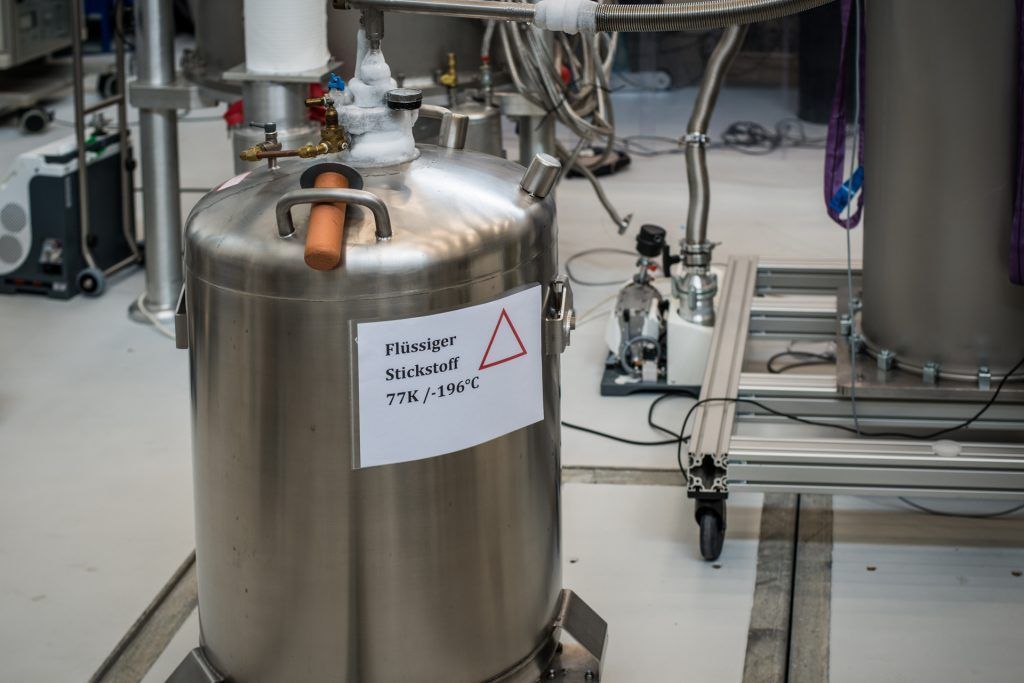
In einer Uni gibt es einen kleinen Raum für Stickstoffbehälter. Dort wurde eine Messstelle montiert. Da es keinen Sensor für Stickstoff gab, wurde der Sauerstoffgehalt überwacht. Die Gaswarnanlage wurde nicht gewartet, da der Betreiber der Meinung war, dass man dies bei einer neuen Gaswarnanlage nicht bräuchte. Leider wurde er seitens des Herstellers bzw. Verkäufers auch nicht anders informiert.
Erst gab es das Vorkommnis, dass bei jeder Abfüllung von Stickstoff Alarm ausgelöst wurde. Somit hat keiner der Mitarbeiter einen Alarm mehr ernst genommen. Trotz Alarm wurde der Raum immer wieder betreten. Grund dafür war, dass die Messstelle direkt neben der Entnahmestelle in 20 cm Höhe über dem Fußboden montiert war. Dies war so vom Planer vorgegeben. Nun hängte man die Messstelle an eine andere Stelle (auf Kosten des Betreibers) und die Fehlalarme hörten auf.
Eines Tages ging eine Mitarbeiterin in den Raum und wollte Stickstoff holen, bückte sich und ihr wurde schwindelig. Sie konnte sich dann gerade noch so aus dem Raum retten und die Tür schließen. Man schaute nun bei der Zentrale der Gaswarnanlage im Flur. Der Wert lag bei 20,7 Vol% O2. Ein ganz normaler Wert.
Durch eine Leckage am Stickstoffbehälter lief dieser aus. Die Gaswarnanlage regierte nicht, weil der Ein- bis Zwei-Jahres-Sensor des Herstellers defekt war. Bei Sauerstoff gibt es den Defekt, dass ein Messwert „einfrieren“ kann. Dies führt dazu, dass keine Störungsmeldung ertönt. Durch die fehlende Wartung konnte der Sensor nicht frühzeitig getauscht werden. Es erfolgte auch kein Hinweis dazu.
Wer trägt nun die Schuld? Am Ende wieder der Betreiber, wobei auch der Planer eine Mitschuld hat. Zum einen die falsche Position, zum anderen wären zwei Messstellen bei dieser Problematik sicherer gewesen. Und zum Schluss ist der ausländische Hersteller auch nicht unschuldig, welcher nur Interesse daran hatte sein Produkt zu verkaufen, da dieser keinen Service in Deutschland hat.
Ursachen:
- Fehlende Gefährdungsbeurteilung & Konzept
- Unzureichende Planung der Gaswarnanlage
- Fehlende Prüfung vor der Inbetriebnahme
- Fehlende Wartung
Verbesserungsvorschlag:
- Auslegung der Gaswarnanlage durch einen herstellerunabhängigen Fachkundigen
- Prüfung der Ausführung inkl. Unterlagen und Zulassungen
- Wiederkehrende Prüfung der Unterlagen, besonders der Serviceberichte
Beispiel 6: Gefahrenpotenzial in der Herstellung von Zink
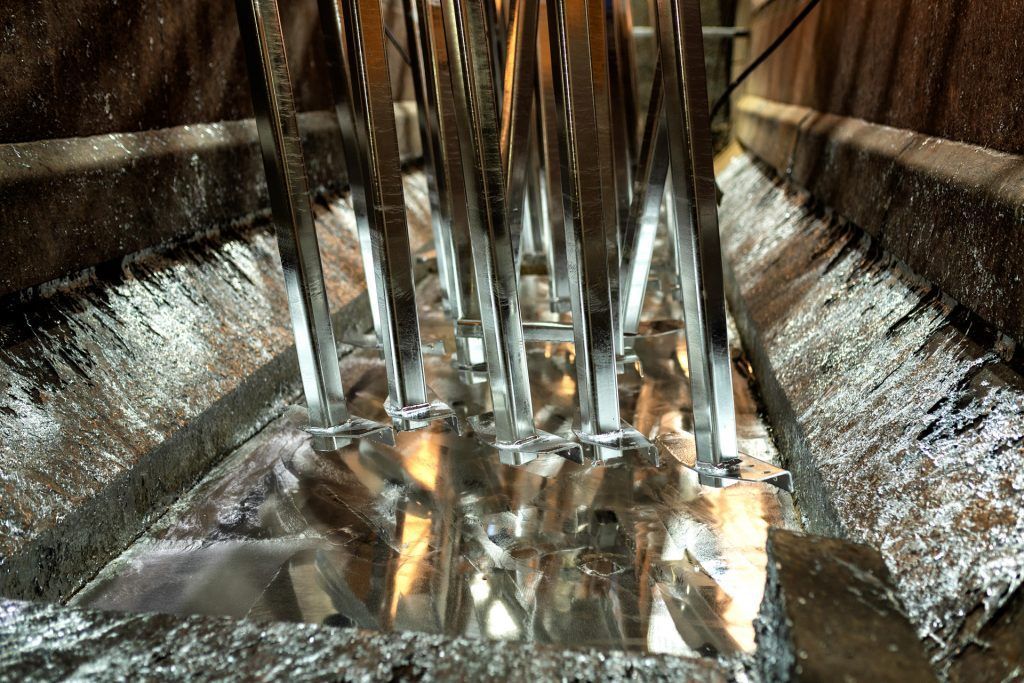
Es wurde zusammen mit einem Hersteller ein Lastenheft für eine Gaswarnanlage zur Überwachung eines hochreaktiven Gases erstellt. Im Anschluss schickte man eine Anfrage mit dem Lastenheft an zahlreiche Anbieter. Da es für diese Gasart nicht sehr viele Anbieter gab, trafen zwei Angebote ein. Man entschied sich für den günstigsten Anbieter der zufällig auch beim Lastenheft behilflich war.
Die Anlage wurde montiert und in Betrieb genommen. Bis dahin funktionierte alles wunderbar, zumindest dem Anschein nach. Mit den Wochen zeigte die Gaswarnanlage aber nicht mehr 0 ppm an. Der angezeigte Wert stieg von Woche zu Woche, bis dieser den Voralarm erreicht hatte. Der Hersteller wurde gerufen. Dieser führte eine Wartung durch, allerdings mit einem völlig anderen Ersatzgas. Soweit nicht ungewöhnlich. Dieses Problem wiederholte sich jedoch und der Zeitrahmen wurde immer kürzer. Nach dem dritten Mal reagierten die Messstellen gar nicht mehr. Es kam zu einem Vorfall in der Produktion und die Gaswarnanlage reagierte nicht. Daraufhin kam erneut der Hersteller. Der nun eingetroffene Mitarbeiter war mit der Situation völlig überfordert, sodass an diesem Tag nichts passierte. Zu einem neuen Termin kam ein weiterer Kollege mit. Nun stellte sich heraus, dass von Beginn an ein falscher Sensor eingebaut worden war. Dieser war für ein ähnliches Gas gedacht, aber nicht für das erforderliche. Es hätte also auch völlig anders ausgehen können. Alleine dieser Ablauf sorgte für mehrere Wochen Produktionsausfall. Kostenfaktor?
Ursache:
- Es wurde ein falscher Anbieter ausgewählt
Verbesserungsvorschlag:
- Hinzuziehen von herstellerunabhängigen Fachkundigen
Beispiel 7: Gaswarntechnik für Kläranlagen
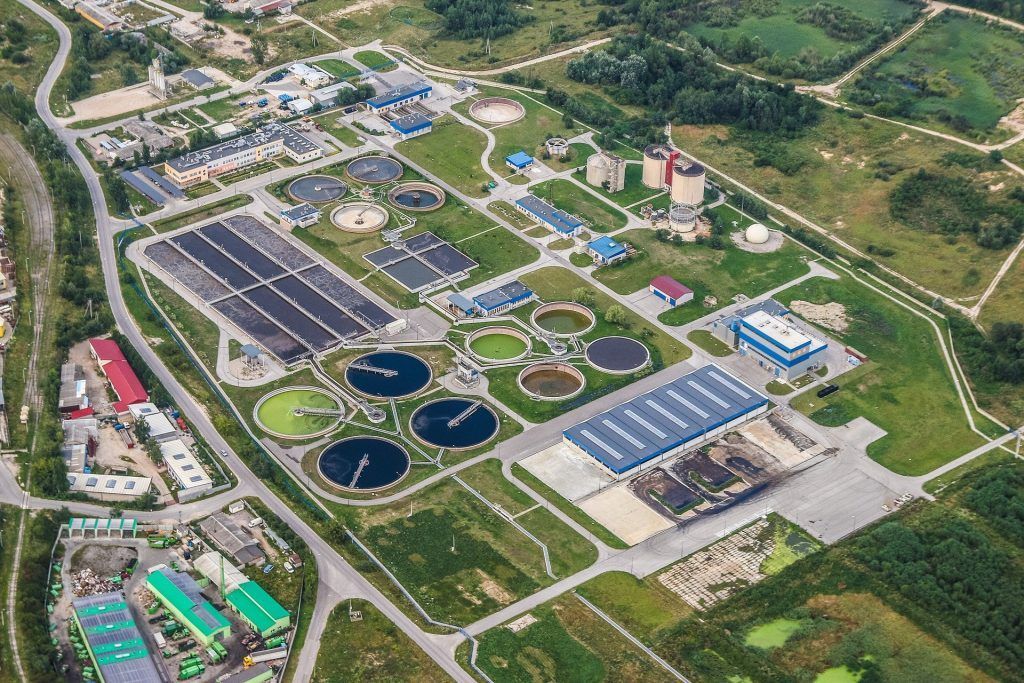
Auf einer Kläranlage sollte im Rechengebäude Methan in der Ex Zone 1 überwacht werden. Dazu holte man sich Vertreter von verschiedenen Firmen und ließ sich Angebote erstellen. Man entschied sich für den günstigsten Anbieter. Dieser installierte die Anlage und sie ging in Betrieb. Einen Monat lang lief alles bis die Fehlalarme anfingen. Die Mitarbeiter mussten in ihrer Freizeit zur Kläranlage eilen. Der Hersteller kam Wochen später, konnte sich das Problem nicht erklären und kalibrierte die Messstelle neu. Es dauert nur Tage und der Alarm war wieder da. Der Hersteller kam wieder und bestellte eine neue Messstelle. Erst nach vier Wochen kam diese und wurde ausgetauscht. Weitere vier bis sechs Wochen funktionierte alles. Dennoch kam der Alarm wieder. Das ganze Spiel begann von Neuem.
Die nächste Messstelle wurde angeblich extra am Sensor mit Harz ausgegossen. So wurde ein Experiment nach dem nächsten vollbracht. Der Vorgang wiederholte sich sechs Mal. Währenddessen war die Gewährleistungszeit abgelaufen. Der Kläranlagenbetreiber entschied sich dazu, die Gaswarnanlage zu entsorgen, wollte aber noch genauer wissen woran es lag. Es kam heraus, dass die Messstelle zwar eine ATEX-Zulassung und eine Baumusterprüfung hatte aber keine messtechnische Funktionsprüfung, wie es vorgeschrieben und notwendig gewesen wäre. Sicherlich wären dort so manche Ursachen des Problems zu Tage gefördert worden. Im Grunde genommen war die Messstelle völlig ungeeignet für diese Anwendung. Teures Lehrgeld für den Betreiber.
Ursachen:
- Unzureichende Planung und Vorgaben an den Hersteller
- Unzureichende Prüfung der Angebote
- Unzureichende Prüfung der Produkte und Zulassungen
- Unzureichende Prüfung vor der Inbetriebnahme
Verbesserungsvorschlag:
- Auslegung der Gaswarnanlage durch einen herstellerunabhängigen Fachkundigen
- Fachlich korrekte Ausschreibungstexte oder Lasten-/Pflichtenhefte
- Angebote fachlich prüfen, vergleichen und auswerten lassen
- Prüfung der Ausführung inkl. Unterlagen und Zulassungen
Beispiel 8: Gaswarnung für die Sauerstoffüberwachung
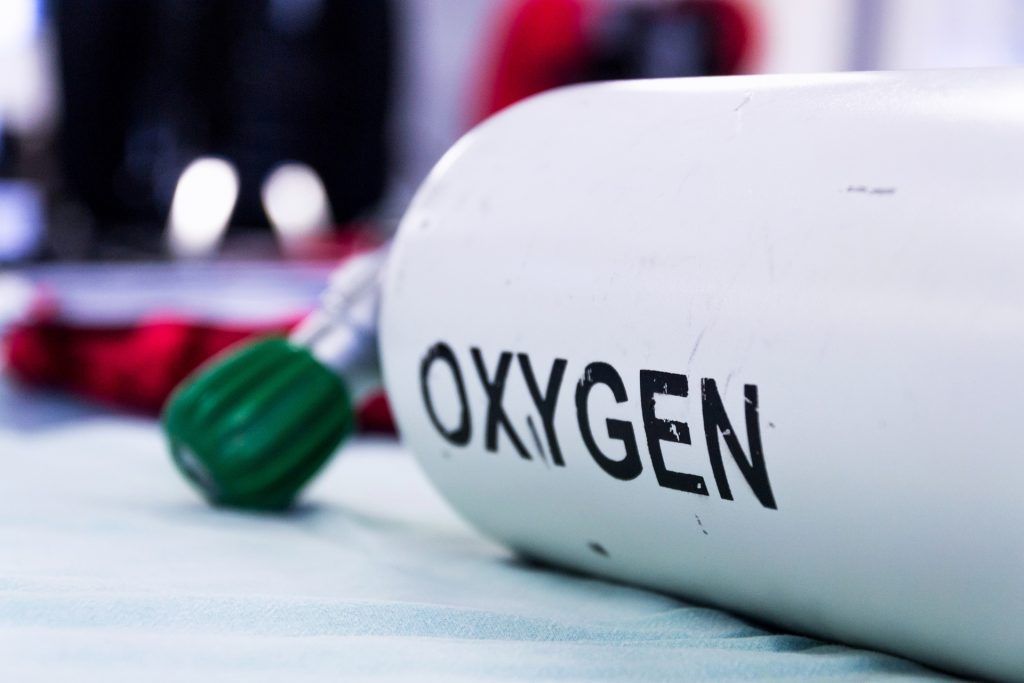
Bei einer verarbeitenden Firma wurde eine Sauerstoffüberwachung benötigt. Dazu holte man sich Vertreter von Herstellern und ließ sich Angebote unterbreiten. Einige schauten es sich vor Ort an, andere nicht. Man entschied sich, wie so oft, für den günstigsten Anbieter. Die Anlage wurde montiert und in Betrieb genommen. Dies ging rund vier Monate gut bis dann plötzlich die gesamte Produktion stehen blieb. Die Gaswarnanlage gab einen Alarm aus und niemand traute sich mehr in den Bereich. Man rief den Hersteller an und bekam keinerlei Hilfestellung. Der Betreiber musste nun die Feuerwehr rufen. Diese führte eine Freigabemessung durch.
Der Betreiber ließ danach die Anlage entfernen und gegen ein anderes Fabrikat ersetzen, welches redundant ausgeführt war. Der Kostenfaktor war jedoch erheblich. Der Produktionsausfall, der Einsatz der Feuerwehr und der Austausch der Gaswarnanlage. Wie es so schön heißt: Hätte man mal jemanden gefragt der sich damit auskennt…
Ursachen:
- Unzureichende Planung und Auslegung der Gaswarnanlage
- Fehlender fachlicher Vergleich der Angebote
- Ungeeignetes Produkt für die Anwendung
- Unpassender Anbieter für die Anwendung
Verbesserungsvorschlag:
- Auslegung der Gaswarnanlage durch einen herstellerunabhängigen Fachkundigen
- Fachlich korrekte Ausschreibungstexte oder Lasten-/Pflichtenhefte
- Angebote fachlich prüfen, vergleichen und auswerten lassen
- Prüfung der Ausführung inkl. Unterlagen und Zulassungen
Beispiel 9: Gasmesstechnik für Labore
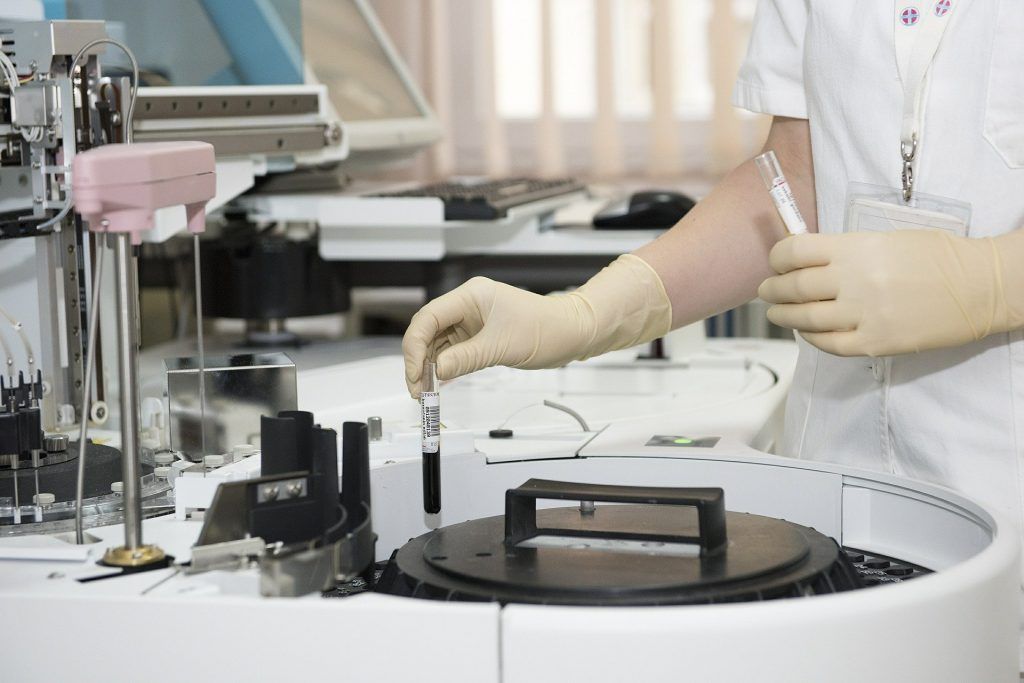
Ein Labor benötigte eine Sauerstoffüberwachung für den Umgang mit Stickstoff, Argon, Helium und anderen Gasarten. Es wurde dort zudem mit brennbaren Gasen gearbeitet.
Man holte sich aus der Entfernung Angebote verschiedener Anbieter ein. Dann dachte man an die Folgekosten und entschied sich für Messtechnik mit langer Lebensdauer: Zirkonium Oxid. Der Hersteller garantierte mindestens fünf Jahre Lebensdauer. Die Anlage wurde montiert und in Betrieb genommen.
Es vergingen ein paar Monate. Irgendwann gab es einen Vorfall, bei dem es Mitarbeitern in dem Labor nicht gut ging. Geistesgegenwärtig verließen alle den Raum und setzten für Tage die Arbeit aus. Nach der Prüfung durch einen Sachverständigen stellte sich heraus, dass die Messstelle nicht mehr reagierte. Diese wurde durch die brennbaren Gase geschädigt.
Das Ergebnis war, dass die Messstelle gegen das herkömmliche elektrochemische Messprinzip ausgetauscht wurde und eine regelmäßige Wartung erfolgte. Kostenfaktor: Ausfallzeit des Labors, Sachverständiger und Austausch der Messstelle.
Ursachen:
- Ungeeignete Planung der Gaswarnanlage im Hinblick auf andere Gase
- Fehlende Gefährdungsbeurteilung
- Falsches Messprinzip der Messstelle, fehlende Hinweise des Herstellers
- Fehlende fachliche Prüfung vor der Inbetriebnahme
Verbesserungsvorschlag:
- Auslegung der Gaswarnanlage durch einen herstellerunabhängigen Fachkundigen
- Angebote fachlich prüfen, vergleichen und auswerten lassen
- Prüfung der Ausführung inkl. Unterlagen und Zulassungen
Beispiel 10: Gasüberwachung für Ammoniak
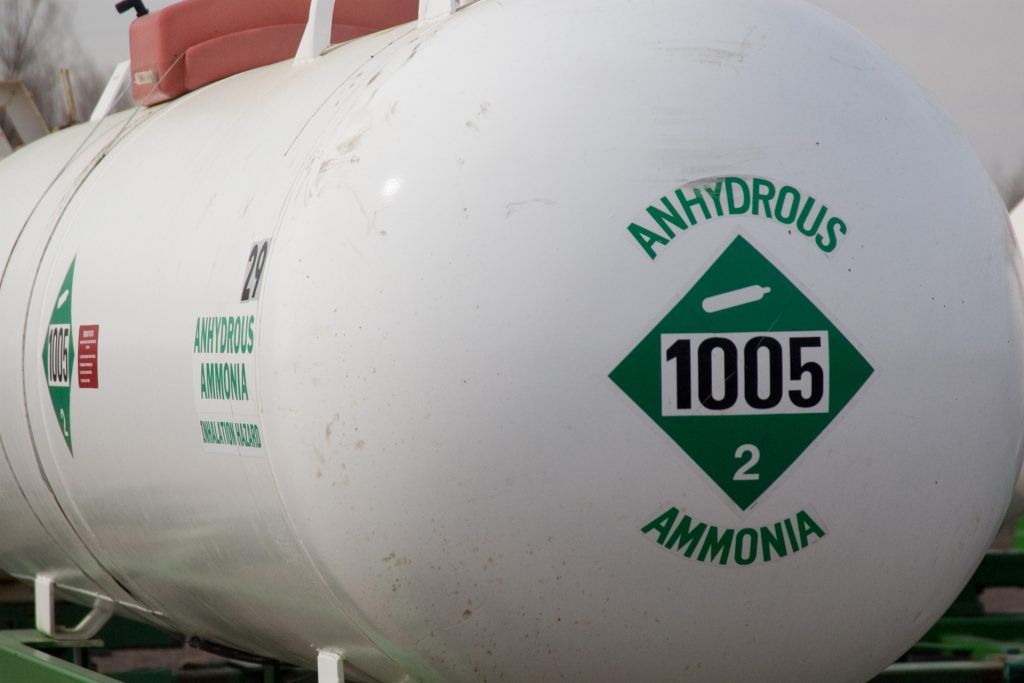
Bei einer Firma sollten Chlor und Ammoniak überwacht werden. Es wurden dazu Angebote eingeholt und eine Anlage beauftragt. Diese wurde montiert und in Betrieb genommen. Alles soweit gut. Danach wurde ein Wartungsvertrag beim Hersteller abgeschlossen. Die ersten Wartungen verliefen optimal.
Es kam dann zu einer Wartung eines anderen Mitarbeiters. Nach Stunden der Wartung meinte er, dass alles fertig sei. Der Servicebericht wurde erstellt und verschwand kurz darauf. Einige Tage später kam es zu einem Vorfall mit Ammoniak. Die Gaswarnanlage reagierte nicht. Weil Mitarbeiter deshalb ins Krankenhaus kamen, wurde alles genauestens geprüft. Es kam heraus, dass der Sensor falsch kalibriert bzw. eingestellt worden war. Man prüfte auch die Chlor-Messstellen. Dort war der Fall bzw. das Problem identisch. Im Anschluss prüfte man beim Wartungspartner. Es kam heraus, dass der Mitarbeiter über keinerlei strukturierte Einarbeitung verfügte und zusätzlich, dass dieser nicht einmal eine Ausbildung hatte. Das bedeutet, dass der Hersteller von Gaswarnanlagen Mitarbeiter ohne eine qualifizierte Einarbeitung und ohne jegliche Berufsausbildung einsetzte. In dem Fall war die Kostenfrage klar, aber dies hätte unter Umständen den Mitarbeitern auch nichts mehr geholfen.
Ursachen:
- Schwer dagegen etwas im Vorfeld zu machen. Hier wären bessere Kontrollen und Strafen des Regierungspräsidiums erforderlich
Verbesserungsvorschlag:
- Wiederkehrende Prüfung der Unterlagen, besonders der Serviceberichte
Hinweis dazu: Stand 2022 gibt es noch Hersteller, welche Mitarbeiter einsetzen, welche über keine Berufsausbildung verfügen, oder über eine völlig Branchenfremde, wie z. B. Industriemechaniker.
Auch ist es bereits ein Standard keine Elektromeister als Gaswarngeräte-Hersteller mehr zu haben und damit offiziell keine Anschlüsse an das 230 V Stromnetz vorzunehmen.
Berücksichtigen Sie dies bei etwaigen Vergleichen und hinterfragen Sie den Ausbildungsstand, wenn Ihnen etwas auffällt.
Generell kann man feststellen, dass der Ausbildungs- und Schulungsstand im Servicebereich besser sein sollte.
Beispiel 11: Wartungen, Funktionsprüfung und Instandsetzungen von Gaswarnanlagen
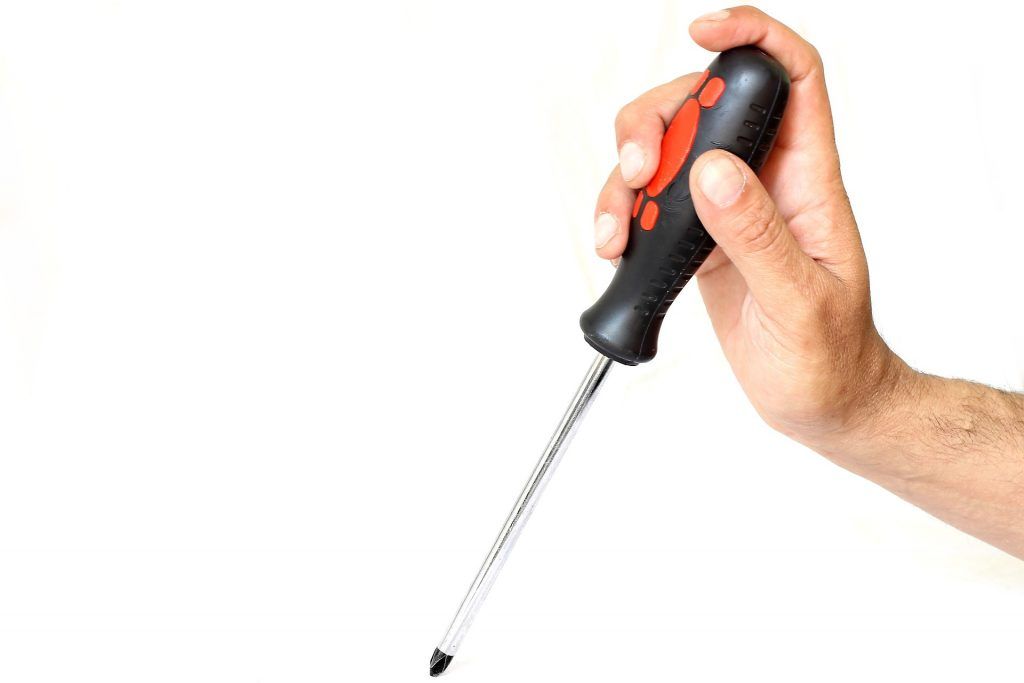
Dieses Beispiel tritt fast täglich in Deutschland auf – in der einen oder anderen Form.
Es besteht eine Gaswarnanlage mit zahlreichen Messstellen. Diese soll wieder gewartet werden. Da Kosten eingespart werden sollen, wird die Wartung entsprechend ausgeschrieben (in manchen Fällen auch nur weit verbreitet angefragt). Den Zuschlag bekommt der günstigste Anbieter. Dieser führt die Wartung durch, die dann mit entsprechenden Plaketten als geprüft gilt. Allerdings kommt zu einem späteren Zeitpunkt heraus (egal ob mit oder ohne Gasalarm), dass die Gaswarnanlage überhaupt nicht vollständig gewartet wurde. Man beaufschlagte die Messstellen mit Prüfgas und klemmte die Meldungen ab, damit es nicht jedes Mal Alarm gibt. Man tat so, als ob die Gaswarnanlage gewartet wird. Eine vollständige Wartung war aber nicht möglich, da man dazu mittels Software auf die Zentrale zugreifen muss und noch dazu ein Passwort der Zentrale benötigt. Somit konnte die Wartung nur zum Teil bzw. unvollständig durchgeführt werden. Der Kunde musste jedoch den vollen Preis einer Wartung bezahlen. In diesem Fall waren keine Sensoren defekt. Es kommt auch gerne vor, dass ganze Gaswarnanlage, zumindest Messstellen, ausgetauscht werden, welche gar nicht defekt sind.
Es hat lange gedauert, bis der Betreiber dies merkte. Erst als es verstärkt zu Fehlalarmen durch defekte Sensoren kam, flog der Fehler auf.
Hier ist der Betreiber in der Pflicht, auch wenn der Auftragnehmer betrugsmäßig handelt.
Ursachen:
- Vergleich von Wartungsangeboten ohne die fachliche Qualifikation dafür
- Fehlende Prüfung der Autorisierung und fachlichen Kompetenz der beauftragten Firma
Verbesserungsvorschlag:
- Wiederkehrende Prüfung der Unterlagen, besonders der Serviceberichte
Tipp: Seien Sie bei der Wartung dabei und schauen Sie sich den Vorgang an, besonders wenn Sie nicht den Hersteller beauftragt haben.
Sollte Sie der Anbieter nach einem Paßwort für die Zentrale fragen, dann ist dies ein Indiz dafür, dass der Anbieter nicht vom Hersteller geschult und autorisiert ist. In diesem Fall „Finger weg“, sonst stehen Sie mit in der Haftung.
Beispiel 12: CO2-Konzentration in Mischbehältern – Quelle aus ASI 8-01
Ein Auszubildender hatte den Auftrag, einen Mischbehälter zu reinigen. Als er in diesen Behälter einstieg, war darin eine CO2-Konzentration in gefahrdrohender Menge vorhanden. Er wurde bewusstlos und konnte den Behälter nicht mehr verlassen. Der Chef wollte den Auszubildenden retten. Obwohl dieser die Gefahr von CO2 kannte, stieg er ebenfalls in den Behälter. Beide konnten nur noch tot geborgen werden.
Beispiel 13: CO2-Unfälle in Brauereien – Quelle aus ASI 8-01
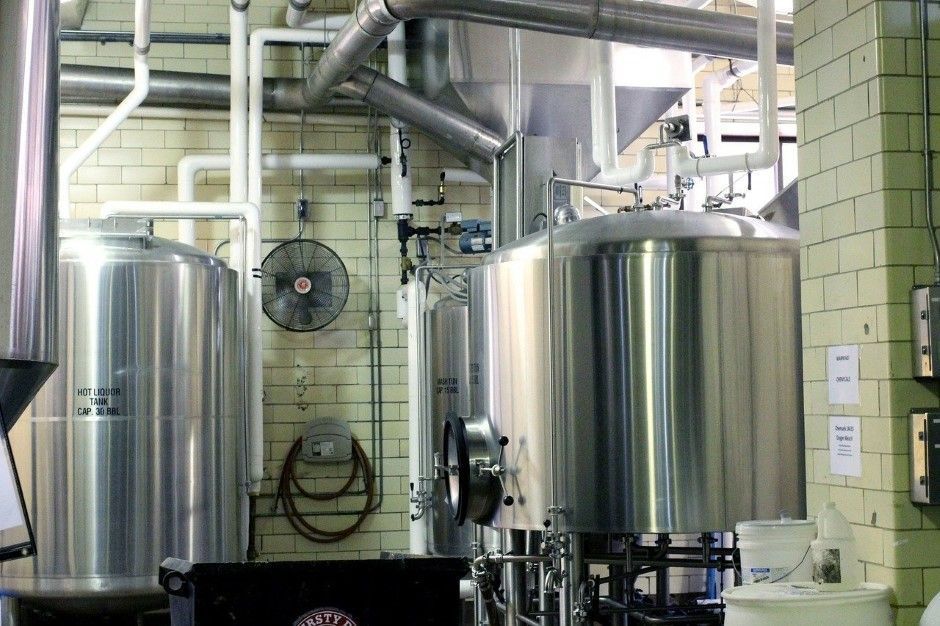
Der Brauereiinhaber wurde bewusstlos aus einem stehenden Weizenbiermischtank geborgen. Kopf und beide Arme des Mannes befanden sich bis zum Oberkörper im Tank. Vermutlich hatte der Mann nach Abfüllung und anschließender Reinigung den Zustand des Behälters überprüfen wollen und sich tief in den Tank gebeugt. Nur zehn Monate später fand man einen Brauereimitarbeiter leblos Kopf voraus im Mannloch eines Drucktanks. Er konnte nur noch tot geborgen werden. Der rekonstruierte Unfallhergang: Beim Umpumpen von Weißbier in einen Drucktank wird ein sogenannter Hefestecker mittels Haken von außen in den Tankauslauf eingesetzt. Nach Reinigung und Vorspannen des Drucktanks sollte das Bier umgepumpt werden. Wahrscheinlich hatte der Mitarbeiter vergessen den Hefestecker einzusetzen und wollte dies nachholen. Nach Ablassen des CO2-Überdruckes beugte er sich tief in den noch CO2-haltigen Behälter hinein, um den Hefestecker manuell ohne Benutzung des Hakens einzusetzen. Dabei erlitt er eine tödliche Vergiftung durch CO2.
Beispiel 14: Notstromversorgung der Gaswarntechnik
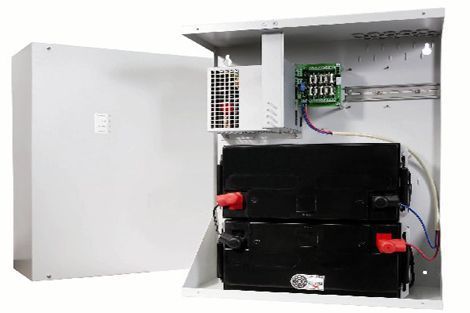
Für ein Projekt wurde eine Gaswarnanlage mit 31 Messstellen und 29 Alarmierungsmitteln geplant und umgesetzt.
Dazu wurde eine Notstromversorgung vorgesehen, welche 2 Stunden lang die gesamte Gaswarnanlage, im Falle eines Stromausfalls, versorgen sollte.
Es wurde CO2 mittels Infrarot-Messtechnik überwacht und die Alarmierungsmittel bestanden aus Blitzleuchten mit Xenon-Blitz und Sirenen.
Soweit funktioniert alles sehr gut.
An einem Tag, nach Feierabend, trat plötzlich ein Gasalarm auf. Erst Voralarm, dann direkt Hauptalarm und zur fast gleichen Zeit (leicht später) viel der gesamte Strom aus.
Nachdem die Notstromversorgung übernommen hatte, dauerte es weniger wie 1 Sekunden und es gab einen kleinen Knall und auch die Gaswarnanlage nebst Meldungen war aus.
Nun ging dies alles so schnell, dass noch keine Alarmierung nach Außen ging und somit niemand informiert wurde.
Ursache war, dass die Stromaufnahme durch die Infrarot-Messstellen und Xenon Blitzleuchten bzw., Sirenen zu hoch war für die Notstromversorgung und deren interne Sicherung löste aus.
Da es sich um einen längeren Stromausfall handelte, kam zu einem späteren Zeitpunkt ein Mitarbeiter, um entsprechend zu prüfen, ob alles in Ordnung ist. Leider lag diesem Mitarbeiter keine Gasalarm-Information/Meldung vor und er lief in die CO2-Havarie hinein.
Sein Glück war, dass es ein Nachbarraum zum eigentlich Ursprungsraum war und deshalb dort die Konzentration nicht so hoch war. Er fühlte sich merkwürdig und wusste dieses Zeichen zu deuten, was ihm das Leben gerettet hat.
Der ganze Vorgang hätte auch anders ausgehen können.
Die Ursache daran war ein Planungsfehler bei der Auslegung zur Notstromversorgung.
Im Anschluss hatte der Gaswarngeräte-Hersteller ein paar Erklärungen zu tätigen, da ein Mitarbeiter des Herstellers die Gaswarnanlage geplant hatte.
Dieses Vorkommnis wurde nicht von seiner Haftpflichtversicherung abgedeckt (ist nicht Bestandteil einer Hersteller-Haftpflicht-Versicherung) und musste komplett von der Firma getragen werden.
Dazu mußte der Betreiber dies vor Gericht mit dem Hersteller erstreiten.
Der Hersteller hat nun die Erkenntnis erlangt, keine Gaswarnanlage mehr zu planen, sondern nur noch das anzubieten, was der Kunde durch seine Gefährdungsbeurteilung oder durch einen Fachkundigen ausgelegt vorgibt.
Ursache:
- Notstromversorgung falsch ausgelegt
Verbesserungsvorschlag:
- Notstromversorgung aufteilen. Eine für die Messstellen und eine für die Alarmierungen.
Beispiel 15: Laboranlagen an einer Universität
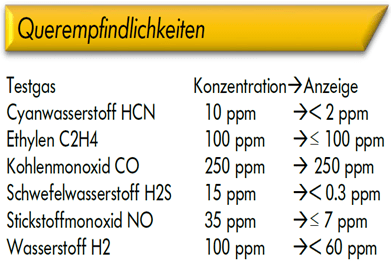
An einer Universität wurden verschiedene Gebäude kernsarniert. Dies betraf auch ein ganzes Gebäude mit Laboren, welche als Auftrags-Forschungs-Labore genutzt wurden.
Für dieses Projekt plante ein Planungsbüro entsprechend alles ein, unter anderem auch die Gaswarnanlagen. Insgesamt wurden 78 Gaswarnanlagen mit über 200 Messstellen in diesem Gebäude vorgesehen.
Bei dem Beispiel dreht es sich um drei Laborräume, welche nebeneinanderliegen.
In allen drei Laborräumen wurde die gleiche Gaswarntechnik eingesetzt mit der Überwachung für dieselben Gasarten.
Für das Beispiel ist wichtig, dass dort Kohlenmonoxid, also CO, und Ethylen, also C2H4, unter anderem vorgesehen wurden. CO wurde mit einem Messbereich von 0-100 ppm installiert und C2H4 mit 0-100 % UEG.
Nun gab es Versuche mit C2H4, wo auch gerne mal etwas davon in geringer Menge austreten konnte. Für die Ethylen Messstelle kein Problem, allerdings ging die Kohlenmonoxid Messstelle jedes Mal auf Hauptalarm und sorgte dafür, dass der Bereich geräumt wurde.
Daraufhin wurde der Hersteller kontaktiert und beschuldigt er hätte schlechte Qualität geliefert. Zusätzlich teilte man dem Hersteller mit, dass man für jeden Tag Ausfall 1.000, – Euro Entschädigung verlangen wird.
Der Hersteller kam und prüfte die Anlage. Anschließend schaute er in den Ausschreibungsunterlagen nach und stellt fest, dass zum einen die Gaswarnanlage und Messstellen einwandfrei funktionierten, zum anderen, dass alles so verbaut wurde, wie es ausgeschrieben bzw. vorgegeben war.
Dann führt der Hersteller aus, dass es zwischen CO und Ethylen eine Querempfindlichkeit von 100 % gibt. Bedeutet, dass wenn 100 ppm C2H4 auftreten auch 100 ppm CO angezeigt werden. Umgekehrt genauso. Da nun die CO-Messstelle einen niedrigen Messbereich in ppm hat und C2H4 einen hohen in Prozent UEG, dürfte klar sein, dass die CO-Messstelle bei jedem Kontakt mit C2H4 einen Alarm auslösen wird.
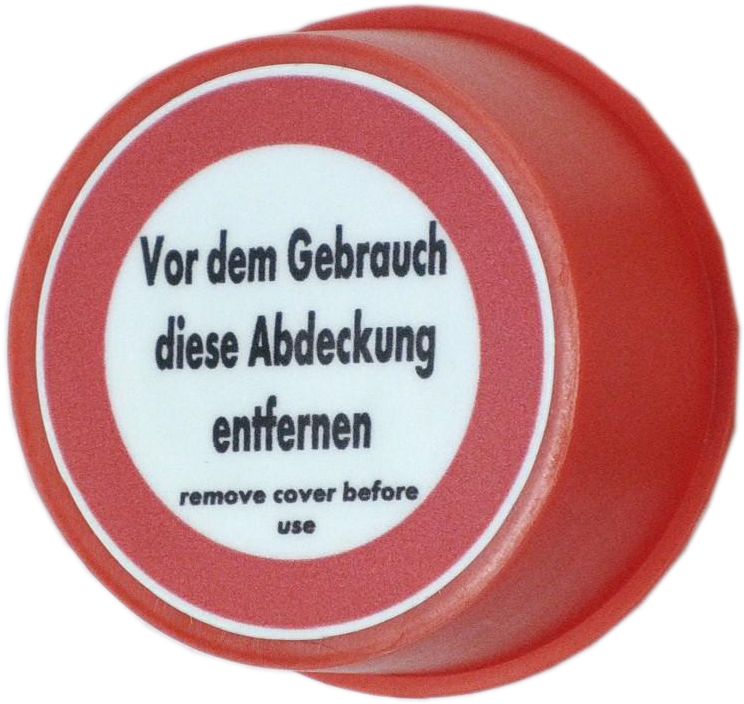
Nun trat man an das Planungsbüro heran und wollte den Schadensersatz vom Planungsbüro. Dies wiederum hatte die Planung von einem anderen Hersteller durchführen lassen, was dem Planungsbüro rein rechtlich aber nichts geholfen hat.
Es stand also am Ende mit vor Gericht:
- Der Hersteller, weil er in der Ausschreibung bzw. Angebot nicht auf die Querempfindlichkeiten hingewiesen hatte
- Das Planungsbüro, weil die Auslegung fehlerhaft war
- Der andere Hersteller, welcher die Auslegung für das Planungsbüro erstellt hatte
Wer die Hauptschuld bekam, ist unklar und nicht bekannt, aber es wurde teuer und bei den Herstellern zahlt für Auslegungs- und Planungsfehler keine Hersteller-Haftpflicht-Versicherung.
Aber es geht noch weiter.
Da das Problem nicht zu lösen war, setzten man auf die CO-Messstellen Abdeckungen und führte die Versuche weiter durch. Dann auf einmal gab es Alarm in den benachbarten Laboren.
Bei der Ursachenforschung kam heraus, dass die Abluftanlage, die Luft von einem Laborraum in den nächsten bläst, statt nach draußen.
Also musste erst einmal alles umgebaut werden und dann gingen die Rechtstreitigkeiten über die Kosten von neuem los.
Ursache:
- Planung/Auslegungsfehler vom Planungsbüro in Verbindung mit dem Hersteller der Planung.
Verbesserungsvorschlag:
- Herstellerunabhängige Auslegung durch eineen Fachkundigen.
Beispiel 16: Ausschreibung Argon-Überwachung
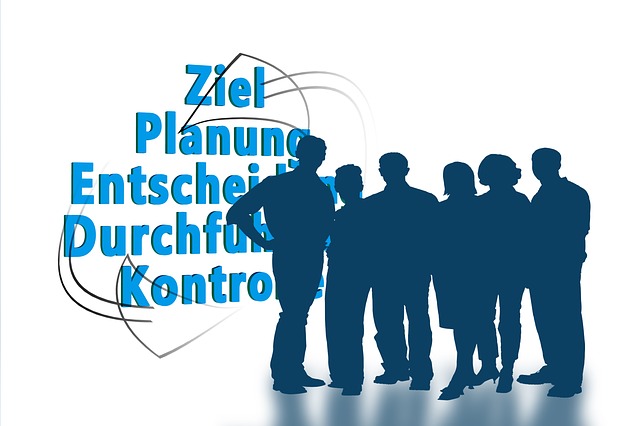
Ein Planungsbüro schrieb eine Gaswarnanlage für 5 Messstellen zur Argon-Überwachung von Produktionsräumen aus.
Dazu holte man sich im Vorfeld von drei Gaswarngeräte-Herstellern entsprechende Ausarbeitung ein und nahm dann sozusagen das „Mittel“ der drei Angebote.
Daraus erstellte man einen Ausschreibungstext, bestehend aus einer Einführungsbeschreibung der Gesamtlage und dann technische Details zu den Produkten. Die gesamte Ausschreibung hatte 11 DIN A4 Seiten.
Als die Ausschreibung raus war, wurde man von einem Hersteller aufmerksam gemacht, dass es diverse Probleme beim anbieten dazu gibt.
Nun suchte man sich einen Fachkundigen, um die Ausschreibung zu kontrollieren, welche aber bereits ausgeschrieben war. Die reinen Anmerkungen und Fehler zu den 11 DIN A4 Seiten beliefen sich auf 9 DIN A4 Seiten. Man kann sagen, dass der Anbieter recht hatte, dass man darauf nicht anbieten kann.
Unabhängig davon wäre die Ausschreibung derartig unnötig teuer geworden, dass man zwar die Anlage mit normalen Bedingungen zu einem Bruchteil hätte bekommen können, mit mehr Auswahl an Anbietern.
Man hat sich bei der Vorbereitung der Ausschreibung so viel Mühe gegeben „neutral“ auszuschreiben, dass man derartige viele Spezifikationen eingebaut hat, welche es dann schwer machten, dass andere darauf anbieten konnten.
Damit hatten es aber auch die drei ursprünglichen Hersteller schwer drauf anzubieten, weil von jedem Textteile bzw. Spezifikationen verwendet wurden.
Am Ende musste die Ausschreibung zurückgezogen und nochmals neu erstellt und veröffentlicht werden.
Diese Kosten und Zeitverzug hätte man sich sparen können, wenn man im Vorfeld herstellerneutral von einem Fachkundigen die kleine Gaswarnanlage auslegen hätte lassen. Aber diese Kosten wollte man nicht investieren, weil man es vom Hersteller umsonst bekommt.
Was dem Planungsbüro bis jetzt nicht klar ist, dass diese mit der Auslegung alleine haftbar sind. Wenn die Ausschreibung nun durchgelaufen und so montiert worden wäre und es wäre etwas passiert, dann hätte keiner der drei Hersteller gehaftet, sondern einzig und alleine das Planungsbüro.
Nahezu keinem Planungsbüro ist klar, was dies bedeutet und dass eine kostenlose Herstellerplanung (ob passend oder nicht) für den Betreiber oder Planungsbüro zu einem existenziellen Problem werden kann und dies dann für eine kleine Gaswarnanlage mit 5 Messstellen.
Ursachen:
- Auslegung vom Hersteller, unpassende bzw. unnötige Aussattung.
- Herstellerneutral augeschrieben aber nicht herstellerneutral ausgelegt.
- Haftung voll beim Planungsbüro.
Verbesserungsvorschlag:
- Gaswarnanlagen immer herstellerneutral von einem neutralen Fachkundigen und nicht von einem Hersteller oder Händler auslegen lassen.
Beispiel 17: Theoretische Planung, praktisch nicht geprüft
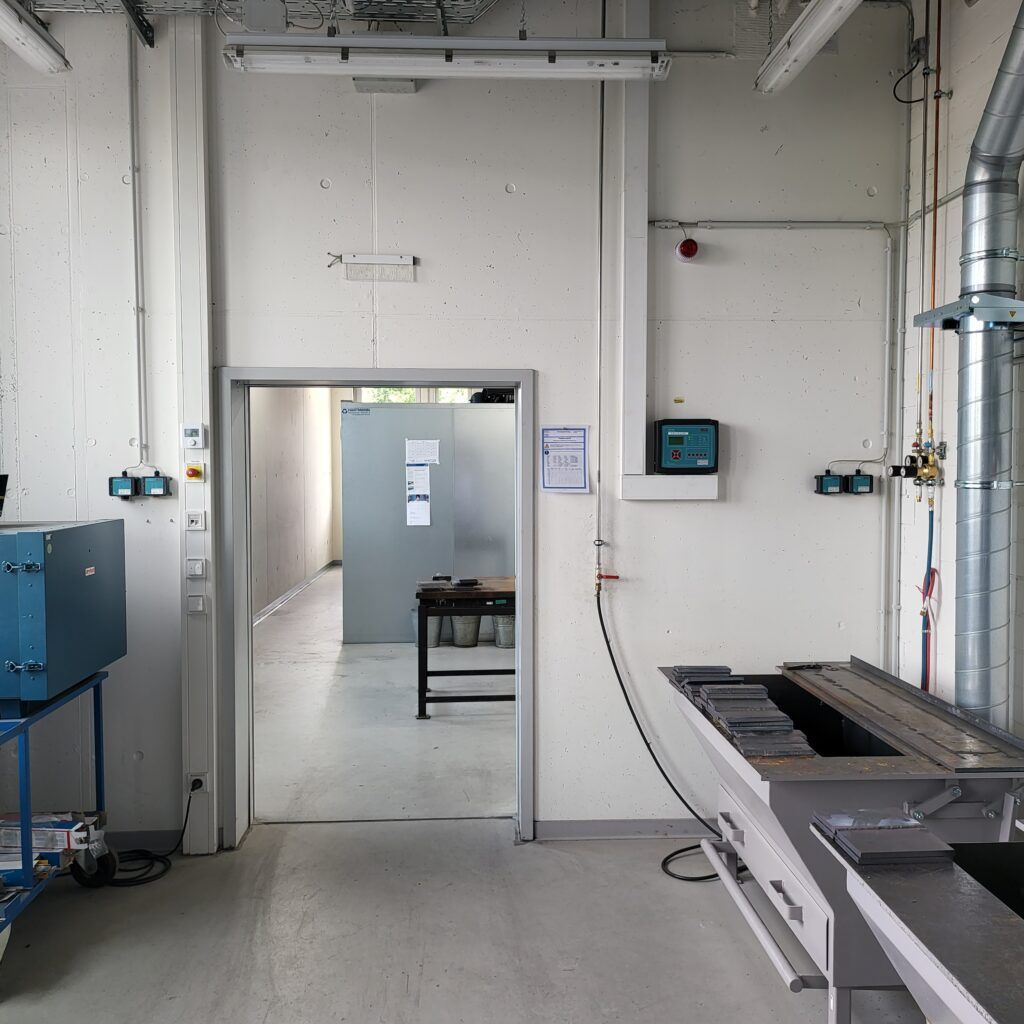
Eine übergeordnete Aus- und Weiterbildungsstelle bekam einen Neubau, welcher von einem Planungsbüro geplant, von einer Fachkraft für Arbeitssicherheit mit einer Gefährdungsbeurteilung versehen und von einem Generalunternehmen ausgeführt wurde.
Nun denkt man, bei so vielen Fachleuten, muss alles passen.
Weit gefehlt, was die Gaswarnanlagen betrifft.
Bei diesem Projekt gibt es nicht eine Gaswarnanlage, sondern sehr viele und auch hunderte von Messstellen. Somit gehen alle Fehler sofort richtig ins Geld. Die Gaswarnanlage ist schon seit zwei Jahren in Betrieb und nur durch einen Zufall wurden wir beauftragt diese, was die Auslegung betrifft, zu überprüfen. Grund dafür waren die extrem hohen Folge- und Unterhaltungskosten durch den regelmäßigen Austausch von Sensoren. Dies bedeutet, dass dort Summen für eine Gasart von 50.000,- Euro rein nur für den Austausch der Sensoren einer Gasart aufgerufen wurden. Und es wurden viele Gasarten überwacht.
Vor dem Ortstermin fand eine Sichtung der Unterlagen statt, welche schon sehr merkwürdig waren. Es gab keine Übersicht über alle Gaswarnanlagen und Messstellen.
Es gab jedoch einen Plan, wo die Gaswarnanlagen eingezeichnet waren, jedoch war dieser komplett fehlerhaft.
Die Unterlagen zur Gaswarnanlage waren unterirdisch. Sowohl die Bedienungsanleitung der Produkte (Datenblätter gab es schon gar keine), wie auch die Serviceberichte zur Inbetriebnahme und Wartung. Auch war nicht ersichtlich, ob die Gaswarnanlagen der notwendigen Norm DIN EN 45544 entsprechen, wir vermuten, nicht.
Beim Ortstermin setzte sich dieser Eindruck fort. Direkt ins Auge viel, dass alle Gaswarnzentrale in dem jeweiligen Überwachungsbereich montiert wurden. Fachliche Planung? Warum hat der Service vom Hersteller nicht schriftlich darauf hingewiesen?
Wenn man dies sieht, dann weiß man sofort, warum die Berufsgenossenschaften und Gesetzlichen Unfallversicherer eine Auslegung durch einen „Fachkundigen“ vorgeben.
Hier war wohl kein „Fachkundiger“ am Werk.
Aber das Beste daran ist: Ein angesehenes deutsches Prüfinstitut hat dort eine Abnahme durchgeführt mit Mängelbericht usw. und dies nicht bemängelt. Läuft.
Dies wird im Nachgang nun sehr hohe Kosten verursachen, da entweder alle Gaswarnzentralen, nebst Kabel, versetzt werden müssen, oder es muss mit externen Anzeigen und Quittiereinheiten gearbeitet werden. Durch die hohe Anzahl an Gaswarnzentralen, ein teures Unterfangen.
Weiter geht es mit dem Messprinzip für Acetylen – C2H2. Hier wurde ein elektrochemisches Messprinzip für eine UEG-Überwachung eingesetzt. Statt des standardmäßig eingesetzten Wärmetöner-Messverfahrens, mit einer Lebensdauer von grob 5 Jahren, wurde ein elektrochemisches Messprinzip mit einer Lebensdauer von grob 2 Jahren eingesetzt. Und dies bei über hundert Messstellen.
Auf das Thema der sicheren Funktionsweise eines elektrochemischen Sensors für eine UEG-Überwachung gehen wir an dieser Stelle nicht näher ein. Hinweis des Herstellers dazu?
Dann befanden sich in Räumen Messstellen für Gasarten, welche gar nicht in dem Raum auftreten konnten. An anderen wichtigen Stellen fehlten diverse Messstellen.
Aber auch die Positionierung war teilweise nicht nachvollziehbar. Zum Beispiel wurde Methan-Messstellen nicht an die Decke montiert, sondern ca. 20-50 cm darunter. Ohne erkennbaren Grund. Hinweis vom Service des Herstellers dazu?
Oder es wurden die Messstellen rechts und links in Fensterhöhe neben die Fenster platziert, was bei einem gekippten oder geöffneten Fenster alles außer Kraft gesetzt wird. Dies wäre schon genug, aber dann stellt man noch geschlossenen Seitenteile/Kabinen direkt davor (sodass man nicht mehr durchlaufen kann). Man könnte spekulieren, dass bis diese Messstellen reagieren, man die Messstellen nicht mehr benötigt.
An dieser Stelle muss man sich die Frage stellen, wie solch eine Fehlplanung passieren kann, wer daran Schuld hat und froh sein, dass das Ganze durch einen Zufall nun aufgefallen und bisher noch nichts passiert ist.
Aber auch an den Service des Herstellers muss man die Frage stellen, ab welchem Punkt ein Hinweis für einen Fehler durch den Hersteller erfolgt? Gar nicht?
Ursachen:
- Ausschreibung nach VOB
- Unzureichende Planung bzw. Auslegung der Gaswarnanlagen
- Fachkraft für Arbeitssicherheit ohne Erfahrung mit Gaswarntechnik
- Prüfinstitut mit fehlender Erfahrung in Sachen Gaswarntechnik
- Unzureichender Gaswarngeräte-Hersteller
- Unzureichender Gaswarngeräte-Service
Verbesserungsvorschlag:
- Planung durch eine fachkundige Person
- Bessere Ausschreibungsvorgaben für geeigneten Hersteller mit notwendigen Zulassungen
- Kontrolle der Planung und Ausführung im Betrieb
Beispiel 18: Universitätslabor
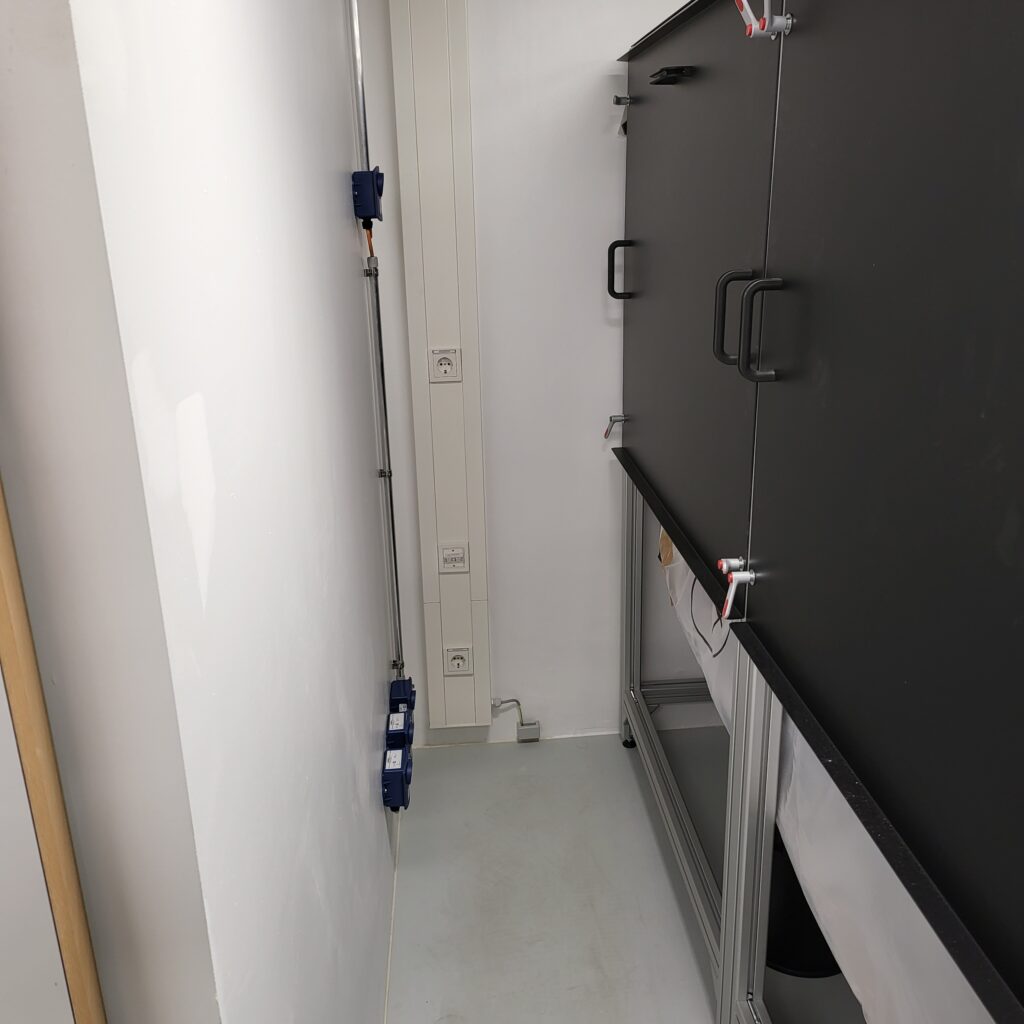
Eine Universität kernsarnierte diverse Räume, um diese nun als Laborräume zu nutzen. Alles wurde soweit geplant ausgeschrieben und ausgeführt. Da mit verschiedenen Gasarten gearbeitet wird, wurde auch eine Gaswarnanlage eingeplant. Diese hat ein deutscher Vertriebsmitarbeiter eines ausländischen Herstellers geplant, welcher bereits diverse Gaswarnanlagen bei der Uni verbaut hat.
Nun begann eigentlich alles ganz banal. Es sollte eine weitere Gasart dazu genommen werden. Für den Vertriebler des Herstellers völlig unproblematisch, da er der Meinung war, das geht ohne Veränderungen und Ortstermin mit den bestehenden Messstellen.
Trotz Hinweis, dass solche Pauschalaussagen nicht sinnvoll sind, blieb er bei dieser Aussage.
Dies zweifelte der Betreiber an und somit wurden wir beauftragt, das Ganze zu prüfen. Leider etwas spät, da schon alles fix und fertig gebaut war.
Eigentlich war es als kurze Ortsbegehung gedacht, um das Thema der zusätzlichen Gasart zu beurteilen, entpuppte sich jedoch als völlige Baustelle, mit einer langen „Mängelliste“.
Ursachen:
- Gaswarnzentrale im Überwachungsbereich.
- Messstellen für eine Raumüberwachung von ca. 70 m2 in einer äußeren Ecke positioniert.
- NH3-Überwachung 20 cm über dem Boden, neben CO2 positioniert.
- Keine Überwachung auf die toxische Wirkung der eingesetzten brennbaren Gase.
- Zeitweise komplett geschlossenen Labormöbel vor den Messstellen.
- Eine einzige Messstelle für Methan, welche auch Wasserstoff überwachen soll.
- Nur eine Messstelle CH4/H2 problematisch, da eine zusätzliche Luftumwälzung an der Decke mit zwei Geräten, welche Luft ansaugen und nach unten blasen.
- Messstellen in Nebenräumen abseits möglicher Undichtigkeitsstellen positioniert, bei vorhandenen ausblasenden Laborgeräten.
- Gaswarnanlage nicht nach DIN EN 45544 für toxische Gase ausgeführt.
- Usw. usw.
Verbesserungsvorschlag:
- Auslegung der Gaswarnanlage durch herstellerunabhängige Fachkundige.
- Beurteilung des Explosionsschutzes.
- Kontrolle der Auslegung, sowie ein Praxisbetrieb möglich ist.
- Kontrolle der Bauabschnitte auf Veränderungen hinsichtlich z. B. Labormöbel, welche plötzlich vor Messstellen positioniert werden.
- Einsatz von Produkten, welche auch entsprechend der notwendigen Normen ausgeführt sind.
- Ausschreibungstexte, welche alle notwendigen technischen Kriterien aufführen, sowie notwendige Zulassungen.
Es ist davon auszugehen, dass die nachträglichen Kosten sicherlich den investierten Kosten in Sachen Gaswarntechnik gleichgestellt sind oder höher liegen werden. In jedem Fall sollte die Gefährdungsbeurteilung dazu überarbeitet und das Ganze geprüft und neu ausgelegt werden. Dies hätte man durchaus vermeiden können. Wie gut, dass es noch angezweifelt wurde. Wie viele Gaswarnanlagen befinden sich wohl aktuell noch an der Uni, welche nicht angezweifelt wurden?
Und das Beispiel zeigt auch: Vorsicht vor den Aussagen einiger Mitarbeiter von Herstellern. Diese sind immer mit Vorsicht zu genießen und zu hinterfragen. Da der Hersteller für eine Auslegung und Beurteilung meistens nicht haftet, sollten Sie sich alles verbindlich und schriftlich geben lassen. Am besten als offizielle Aussage des Herstellers/Firma, nicht nur von einem einzelnen Mitarbeiter in Form einer einfachen E-Mail, denn diese wird Sie nicht absichern.
Beispiel 19: Hotel
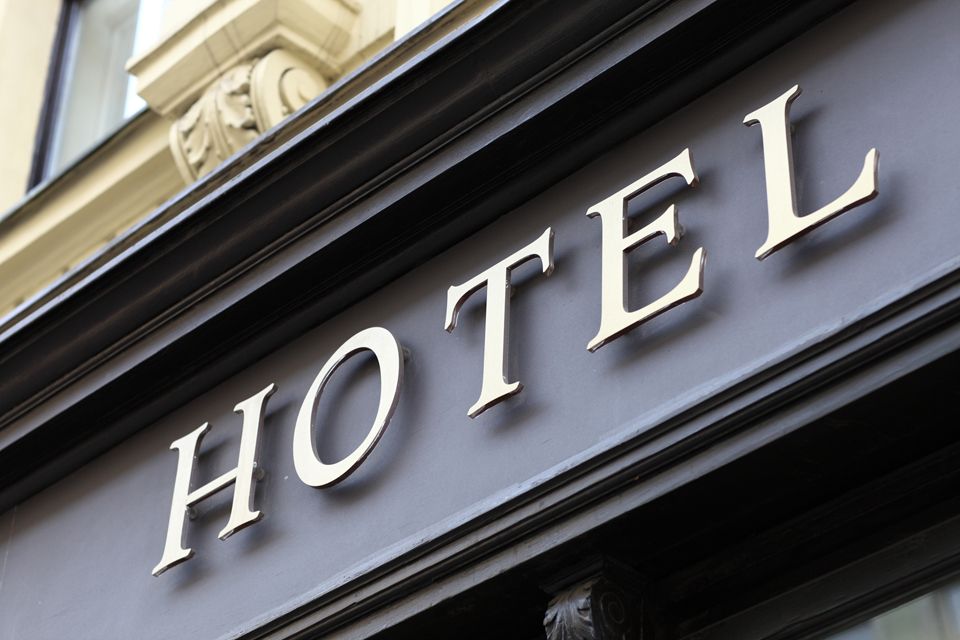
Ein Hotel in Baden-Württemberg, mit etwas über 80 Betten, besitzt ein mit Erdgas betriebenes BHKW. Hier wird mittels einer Gaswarnanlage Erdgas überwacht.
Die Gaswarnanlage wurde 2020 von einer Klima- und Gebäudetechnik-Firma eingebaut, interessanter Weise mit dem Text einer Tiefgaragen-Gaswarnanlage auf der Rechnung.
Die ausführende Firma befindet sich alle zwei Jahre beim Hersteller auf einer entsprechenden Service-Schulung und scheint neben seiner Kerntätigkeit (Gebäude- und Kälteanlagen), im Schwerpunkt Gaswarnanlage in Tiefgaragen und Kälteanlagen, zu verbauen.
Als Messprinzip für die BHKW-Überwachung wurde das Wärmetöner/Pelistor Messprinzip für die Methan-Überwachung gewählt. Eine Überwachung auf Kohlenmonoxid findet nicht statt.
Es erfolgte bei der Inbetriebnahme keine Kalibrierung und Justierung der Sensoren/Messstellen und gemäß Unterlagen auch keine Prüfung. Auch die Dokumentation der Inbetriebnahme entsprach nicht den seit 2016 vorliegenden Normen und Regelwerken.
Es dauerte nicht lange und das Hotel hatte den ersten Fehlalarm.
Das Hotel wurde komplett geräumt, um dann einen Fehlalarm der Gaswarnanlage durch die Feuerwehr festzustellen.
Im Nachgang fand eine Wartung der Gaswarnanlage durch die Klima- und Gebäudetechnikfirma statt.
Die Dokumentation dazu ist sehr unvollständig und lässt wenig Nachvollziehbarkeit zu.
Es dauert nicht lange und der nächste Fehlalarm folgte. Dies zogt wiederum eine Wartung nach sich.
Aber auch danach gab es wieder einen Fehlalarm.
Der Händler empfiehlt nun dem Hotel das aktuelle Messprinzip Wärmetöner gegen ein Infrarot-Messprinzip auszutauschen. Natürlich kostenpflichtig und unabhängig vom vorliegenden Schaden durch Feuerwehrkosten nebst Imageschaden bei den Gästen.
Das Hotel ist nun so verunsichert, dass es die Gaswarnanlage entfernen möchte, da die Kosten jedes Fehlalarms nicht im Verhältnis zur Gaswarnanlage stehen.
Wenn statt Fehlalarme nun keine oder zu späte Alarme erfolgen würden, wer würde nach aktuellem Stand die Hauptschuld tragen?
Der Betreiber, also das Hotel.
Nicht der Händler, welcher anscheinend wenig Ahnung hat was er dort tut. Und auch nicht der Hersteller, welchen den Händler anscheinend völlig unzureichend geschult hat, oder die ausführende Person gar nicht geschult wurde.
Warum? Man hat nicht den Hersteller beauftragt und sich nicht die notwendige Qualifikation der beauftragten Firma nachweisen lassen.
Aktuell kann das Hotel froh sein, dass es sich um Fehlalarme handelt. Diese kommen das Hotel zwar teuer zu stehen und der Imageschaden bei den Hotelgästen dürfte auch nicht ohne sein, aber wenn der Alarm zu spät kommen würde, wären die Probleme gänzlich anders.
Egal wie man es dreht und wendet, das Hotel bzw. den Betreiber wird die Hauptschuld treffen, aber die Ursache liegt beim Hersteller der Gaswarngeräte und dessen Vertriebsform bzw. Schulungen.
Ursachen:
- Auslegung der Gaswarnanlage nicht durch einen Fachkundigen.
- Es fehlt die CO-Überwachung.
- Fehlende Kalibrierung bei der Inbetriebnahme, egal was der Hersteller dazu sagt.
- Unsachgemäße Kalibrierung bei der Wartung.
- Geeigneter Hersteller für diese Anwendung?
- Direkter Einsatz von Infrarot-Messstellen?
- Unzureichende Serviceberichte.
- Unzureichende Schulung beim Hersteller/durch den Hersteller?
Verbesserungsvorschlag:
- Auslegung der Gaswarnanlage durch einen Fachkundigen.
- Einsatz eines geeigneten Herstellers/Produkte.
- Überwachung aller notwendigen Gasarten.
- Einsatz geeignete Messprinzipe.
- Hersteller Service beauftragen (vor dem Kauf prüfen ob vorhanden).
- Qualifikation von Händlern nachweisen lassen.
- Separate Schulungen zwischen Technik und Grundlagen.
- Hersteller-Schulungen verbessern.
- Bessere Vorlagen z. B. Service-Berichts-Vorlagen für geschulte Händler.
- Beachtung und Einhaltung der aktuellen Normen und Regelwerke im Hinblick auf die Durchführung von Wartungen.
Schauen Sie immer mal wieder vorbei, wir ergänzen die Beispiele regelmäßig.
Beispielbilder und alte Produkte
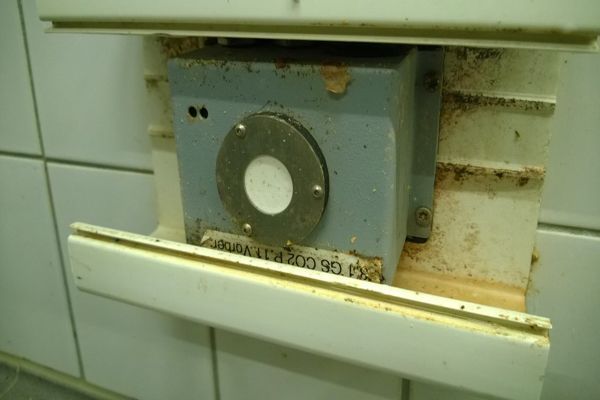
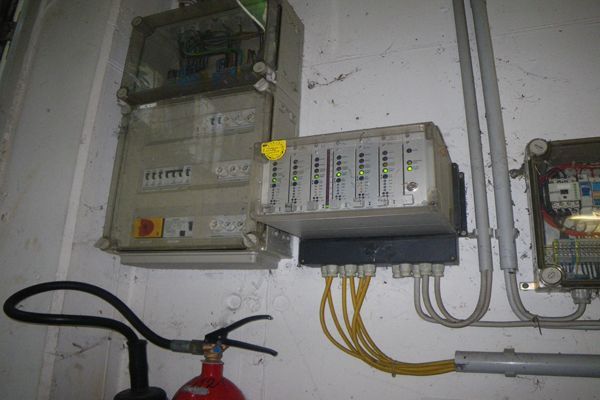
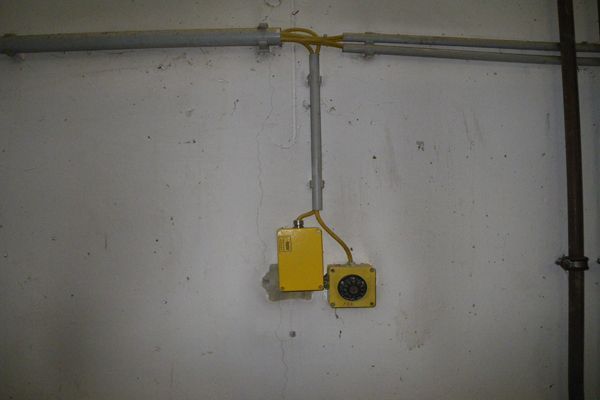
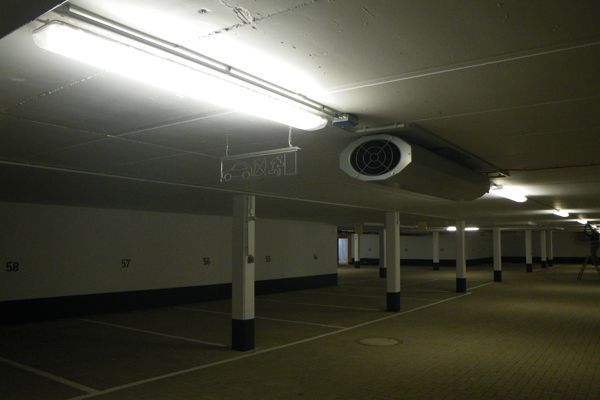
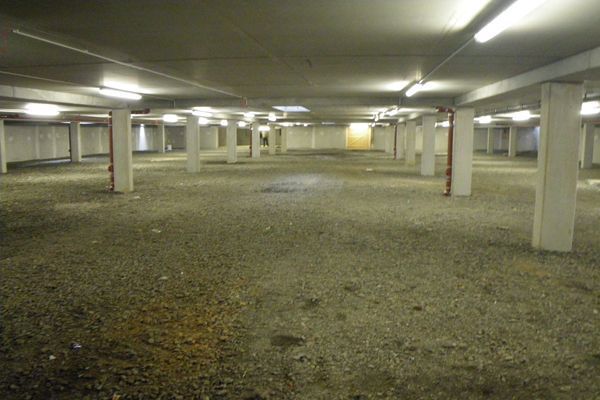
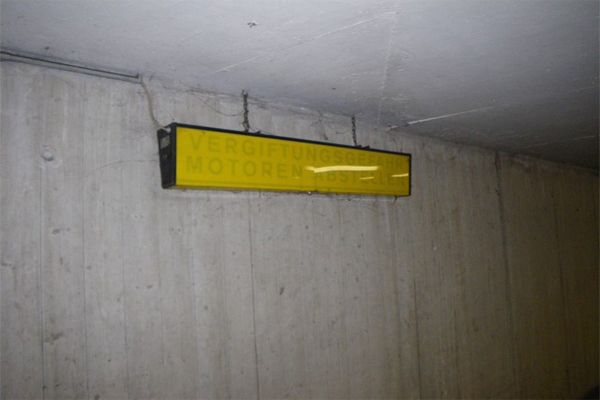
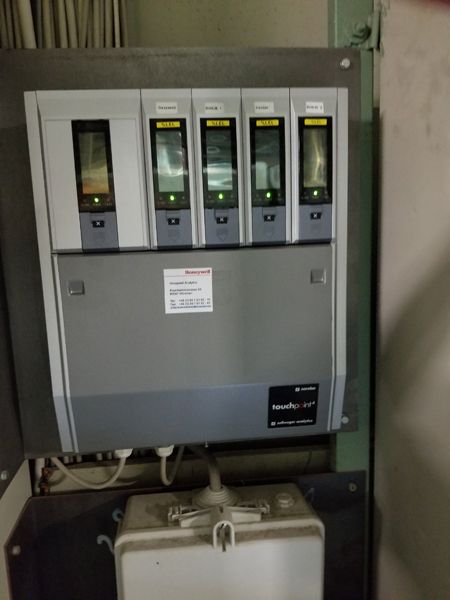
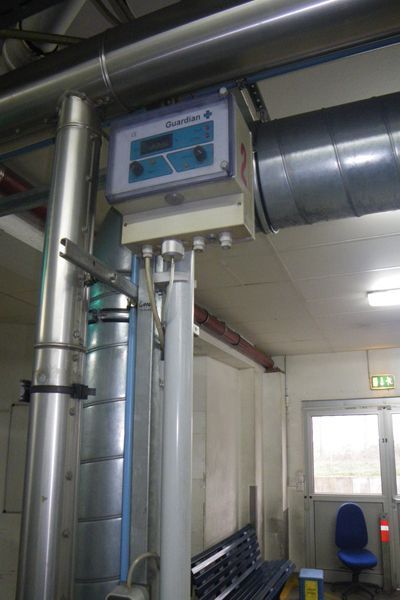
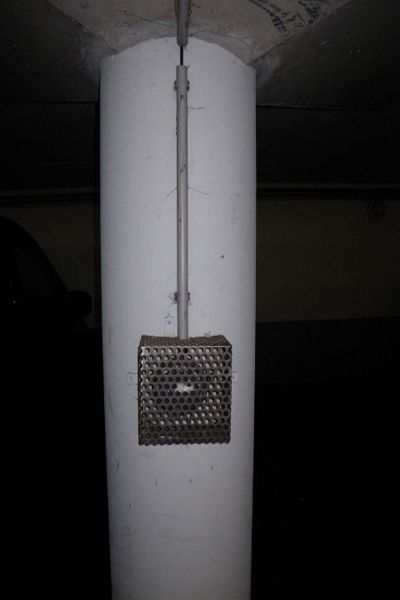
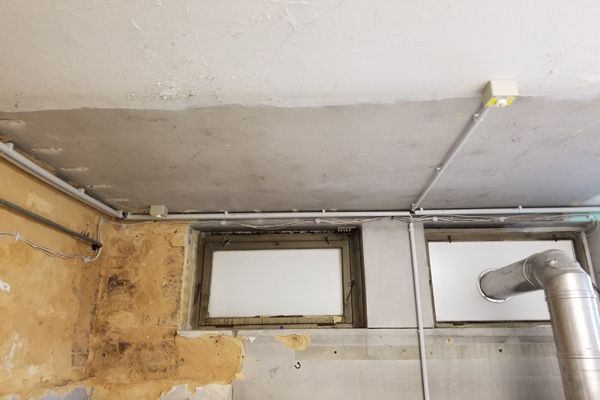
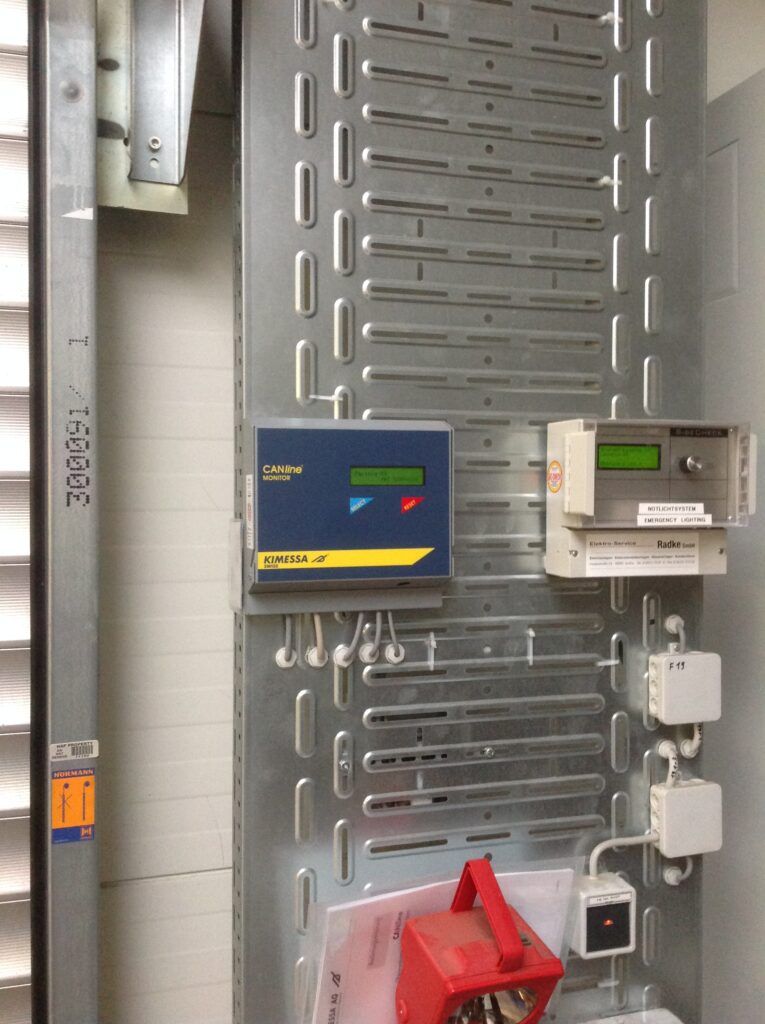
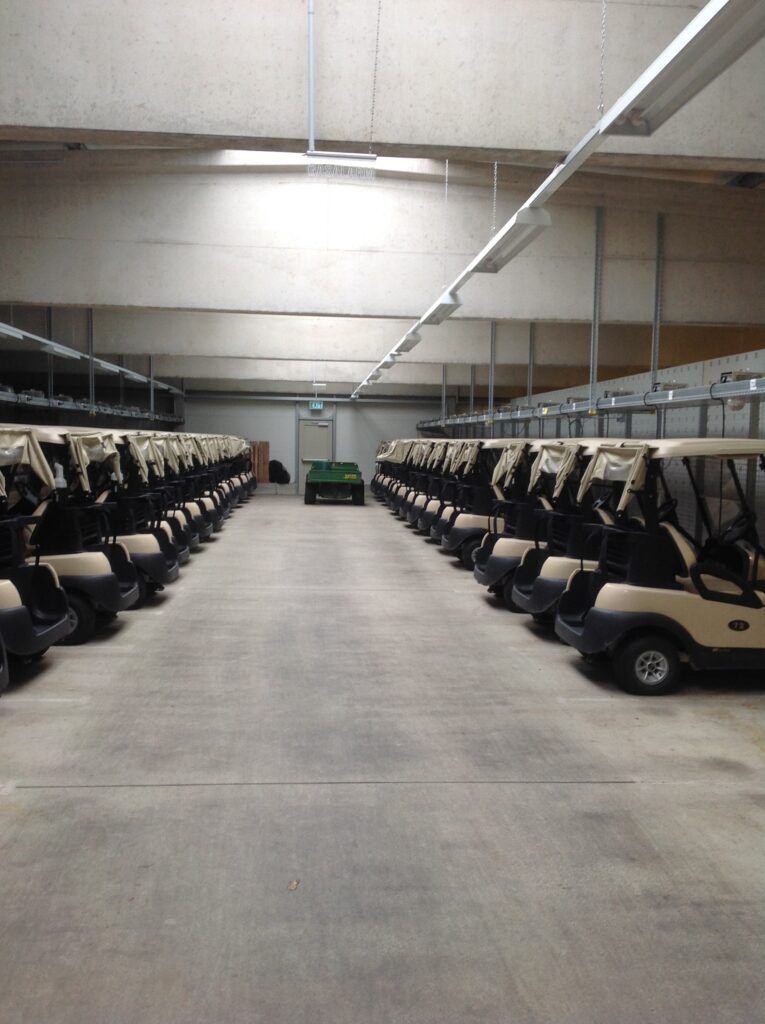
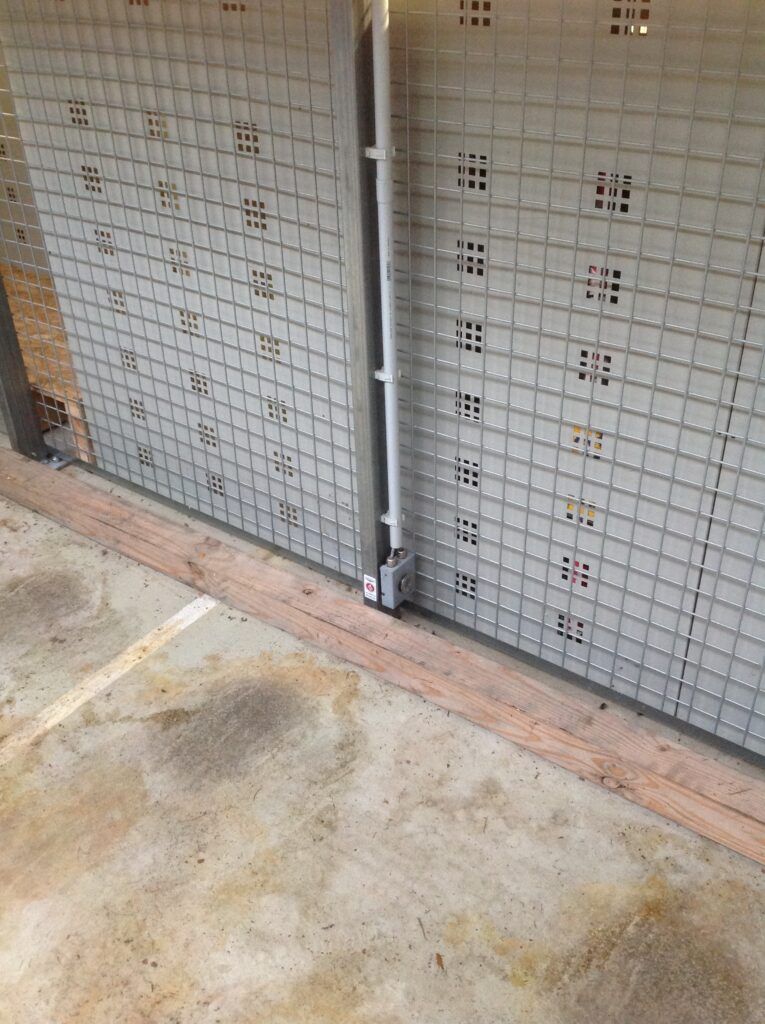
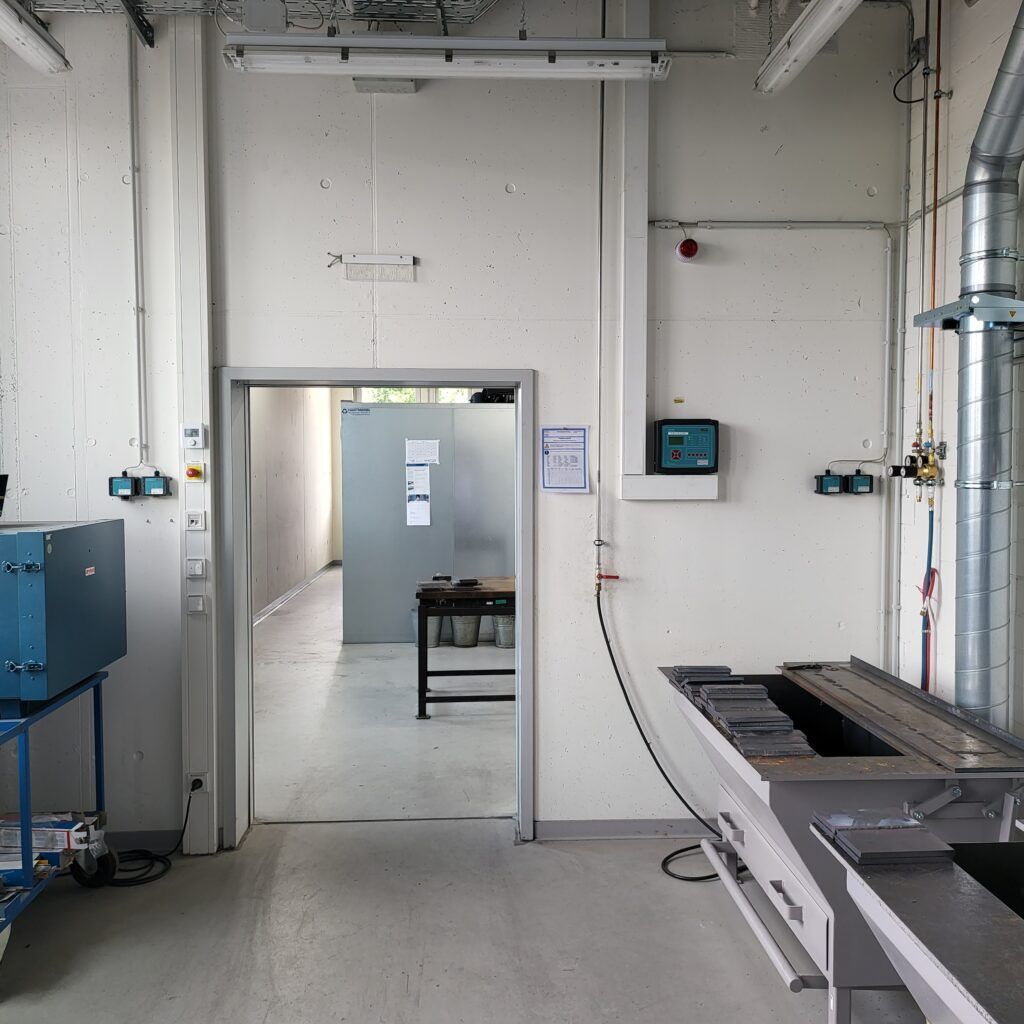
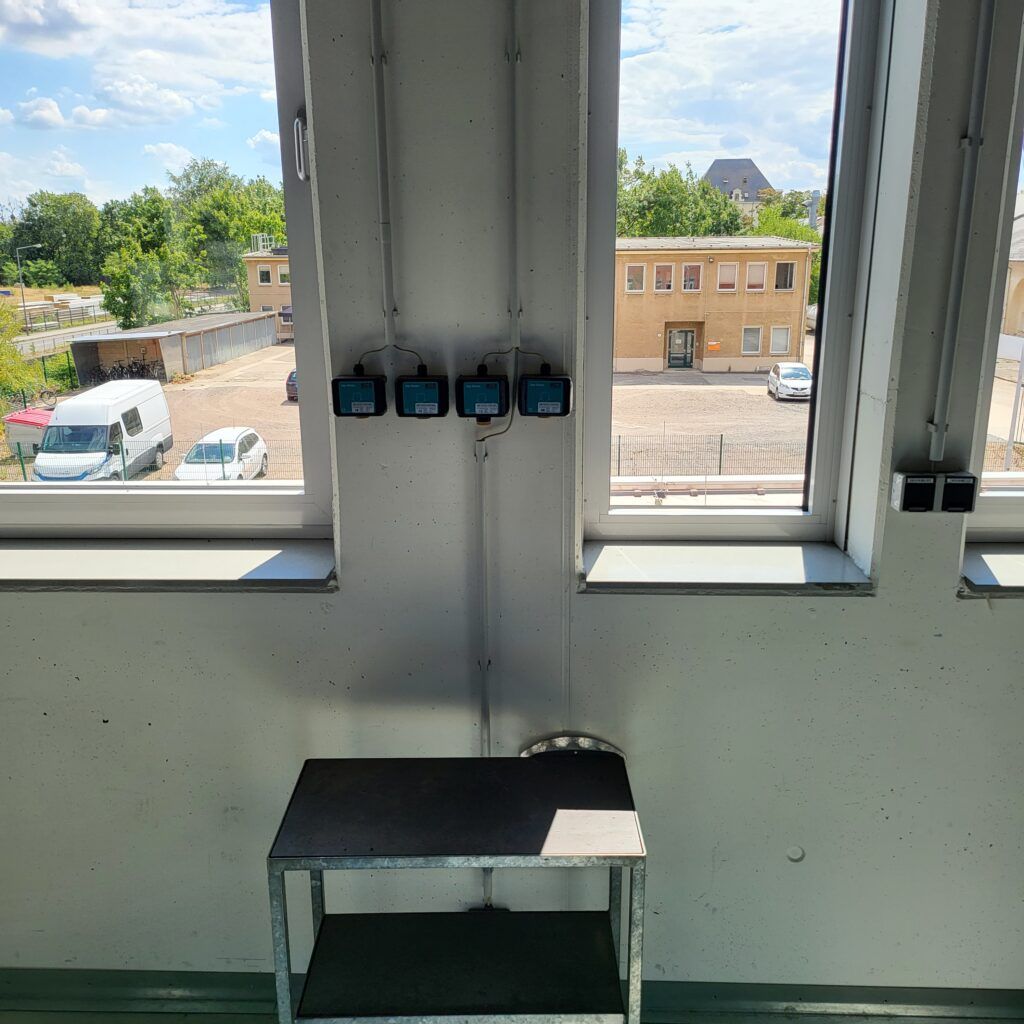
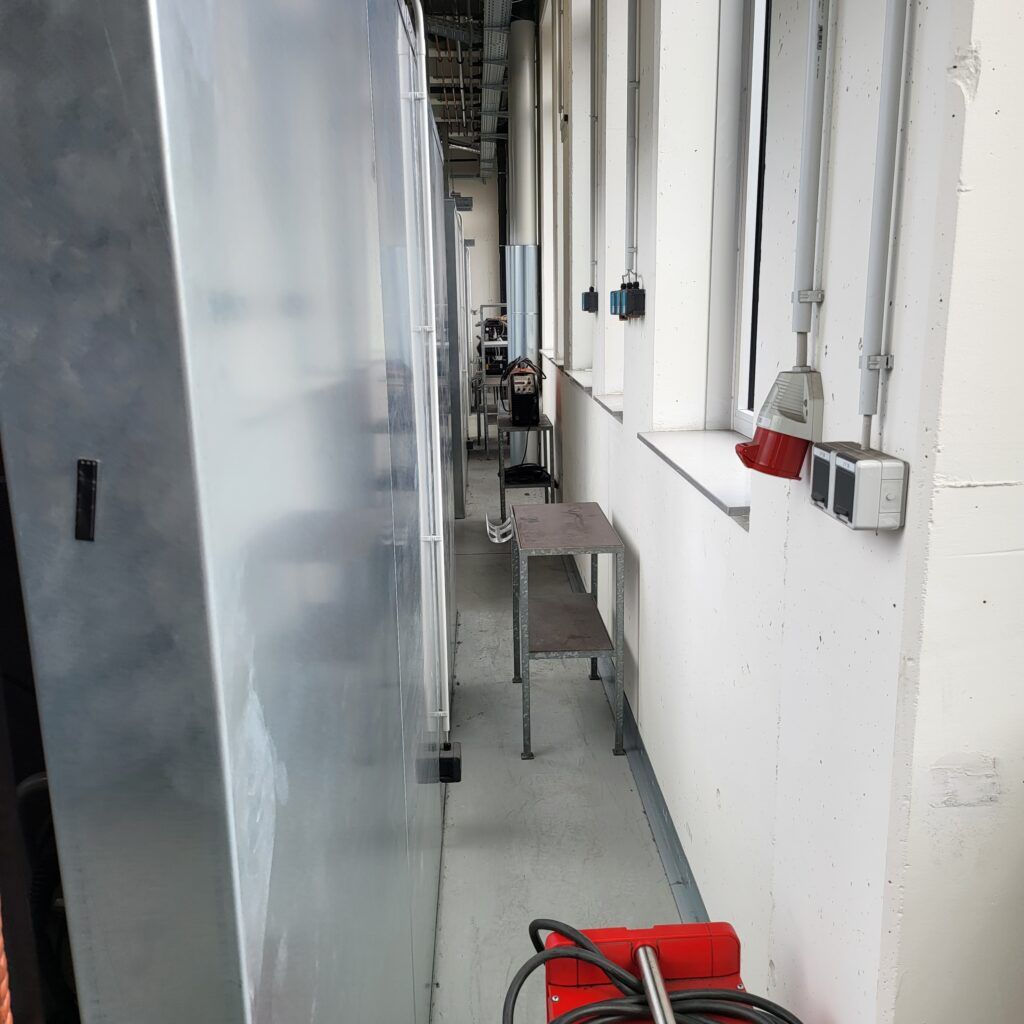
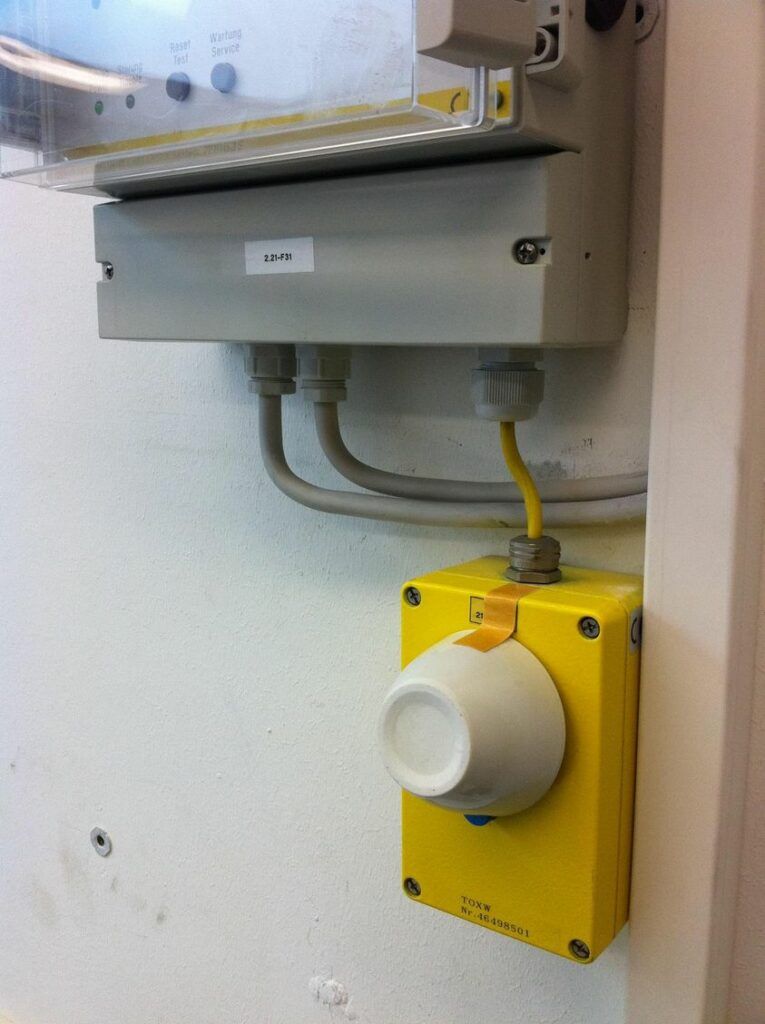
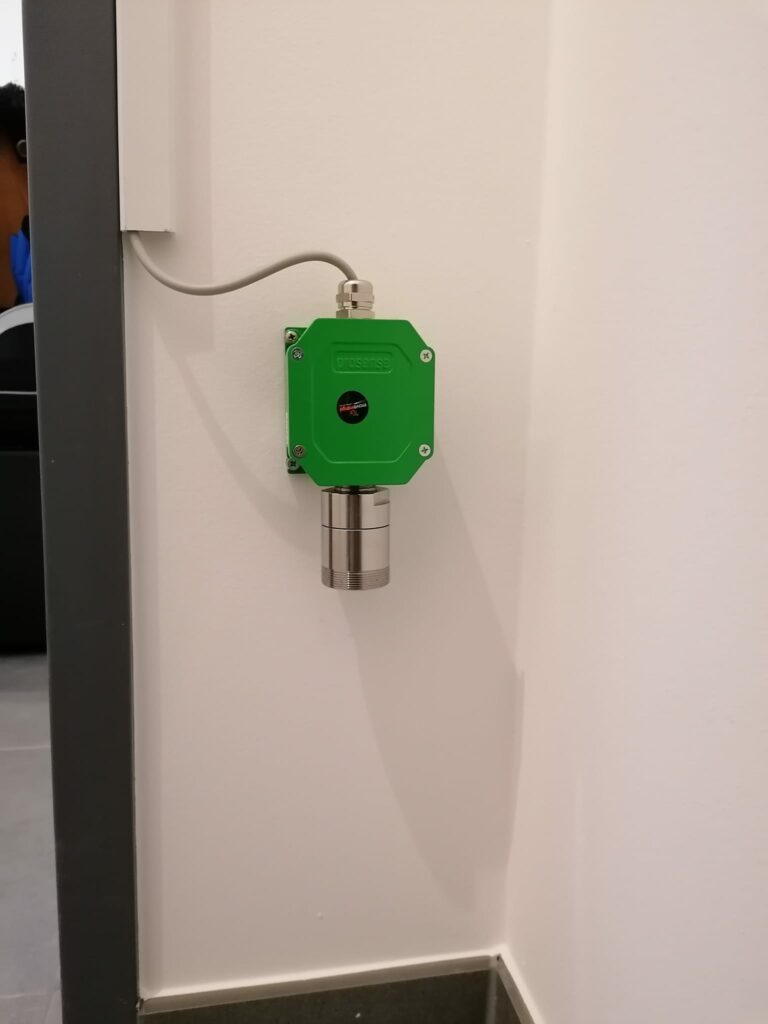
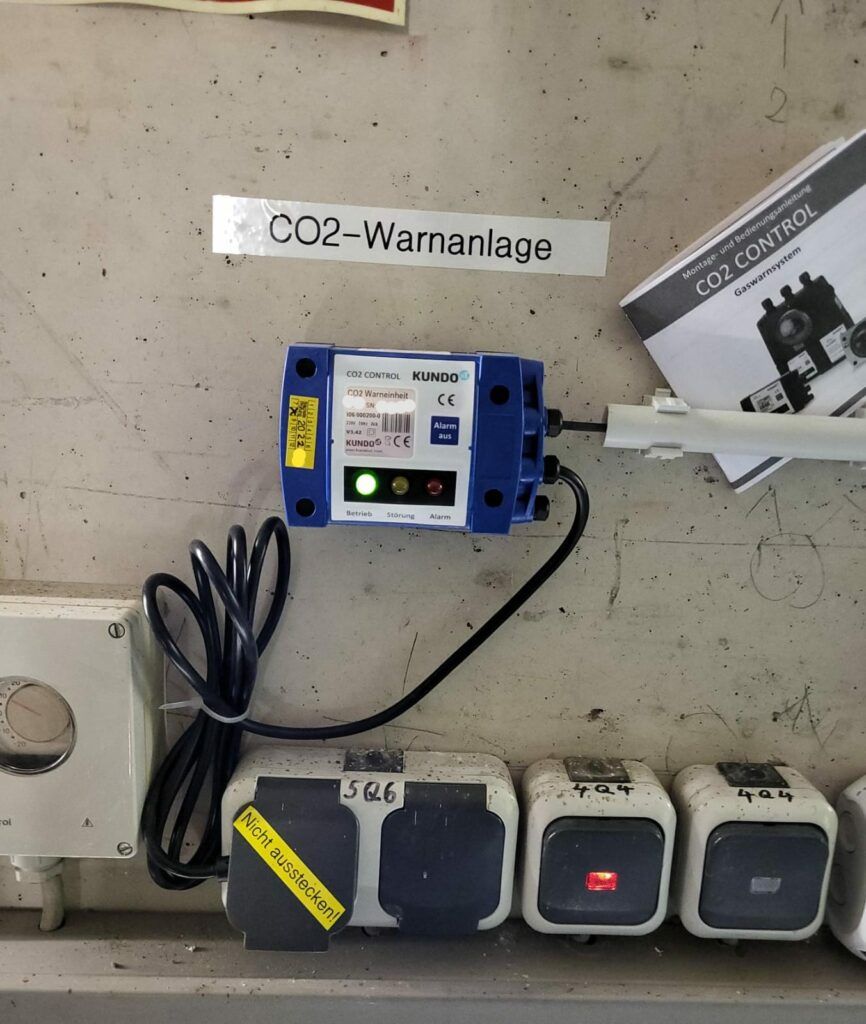
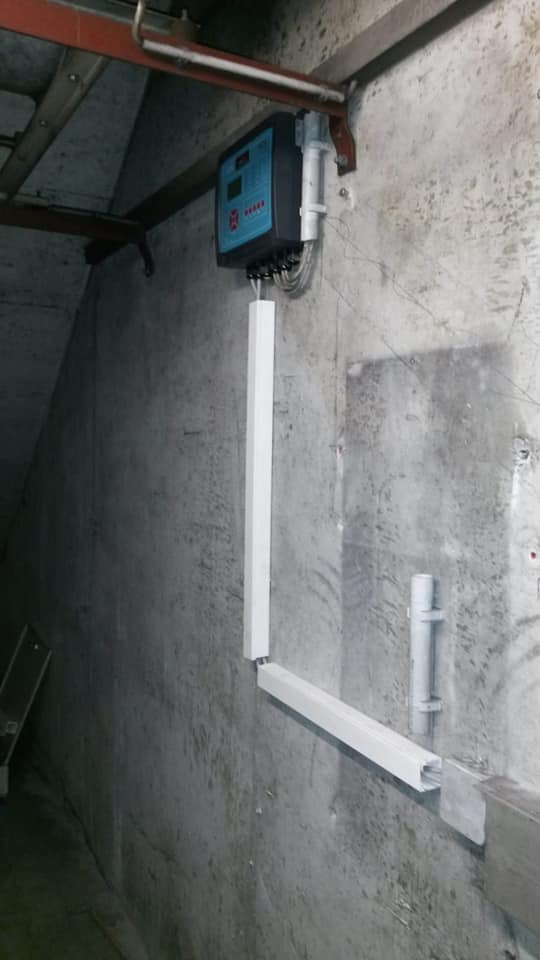
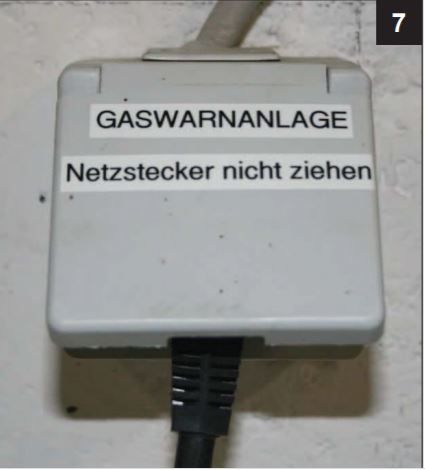
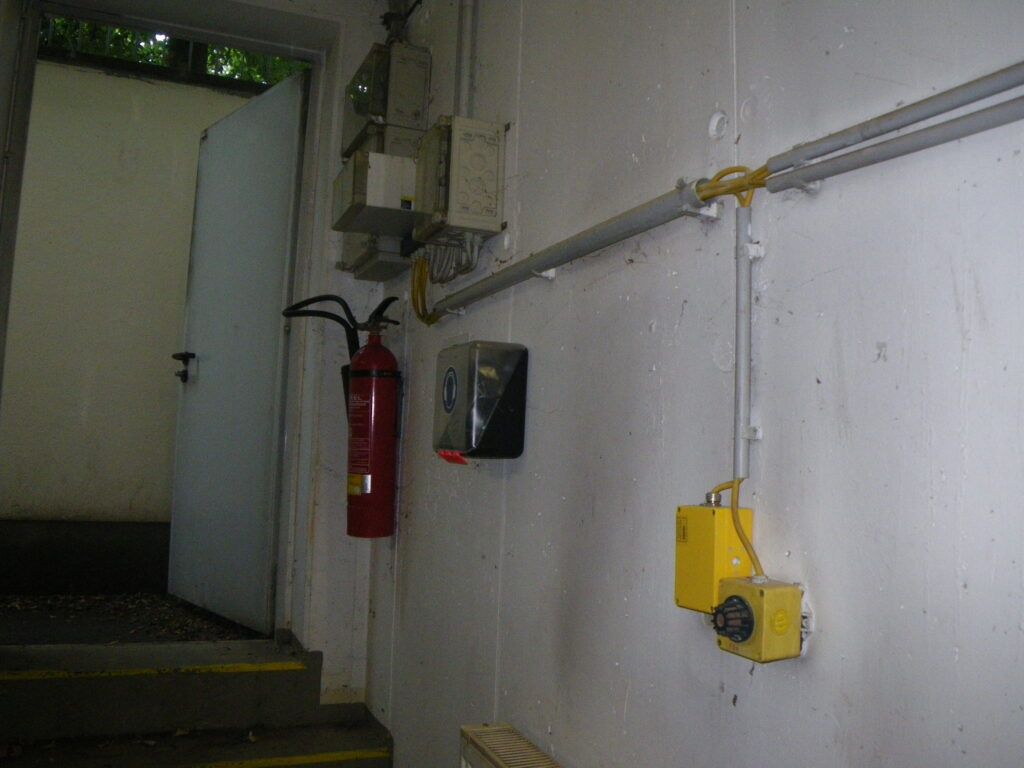
Die Entwicklung der Gaswarngeräte-Messstellen
Hier folgend eine Übersicht über die verschiedenen Bauformen von Gaswarngeräte-Messstellen mit der Angabe wann diese jeweils gebaut wurde. Das Baujahr ist aber nicht das Konstruktionsjahr, welches teilweise deutlich älter sein kann.
1995
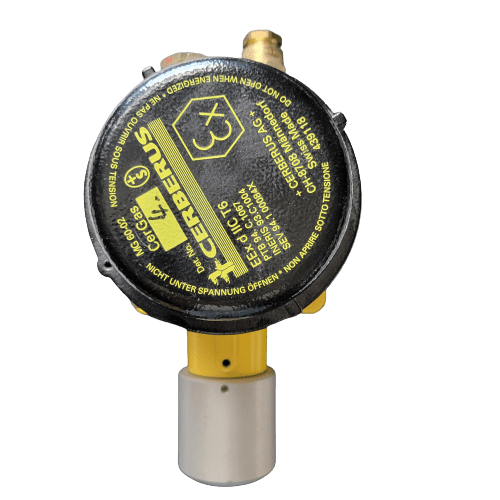
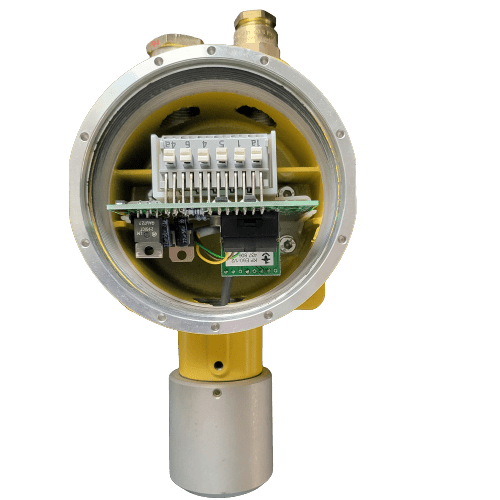
2006
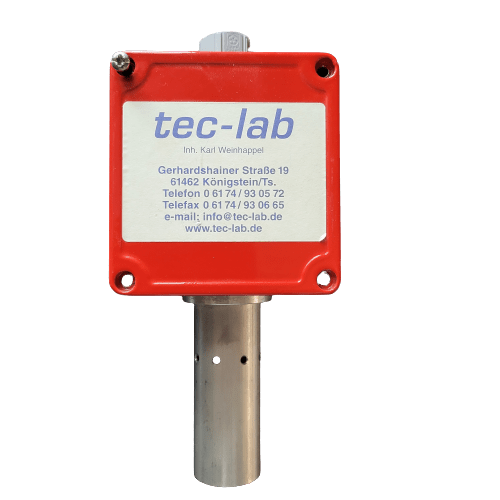
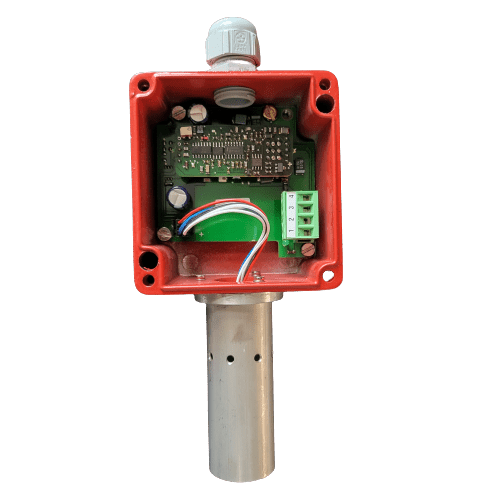
Unbekannt
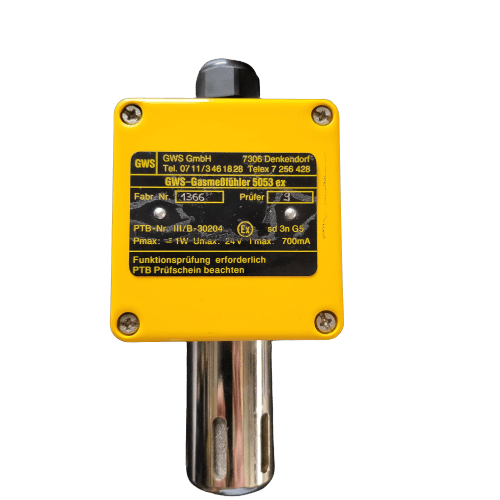
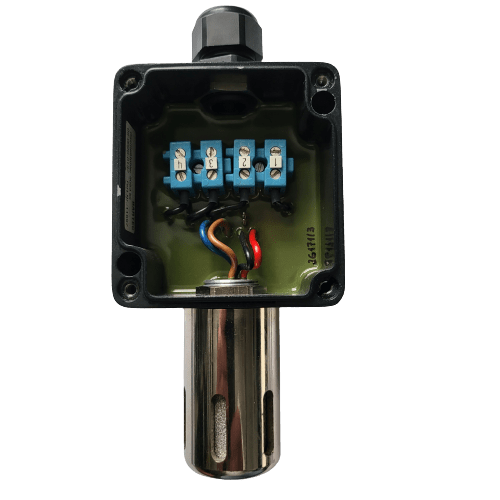
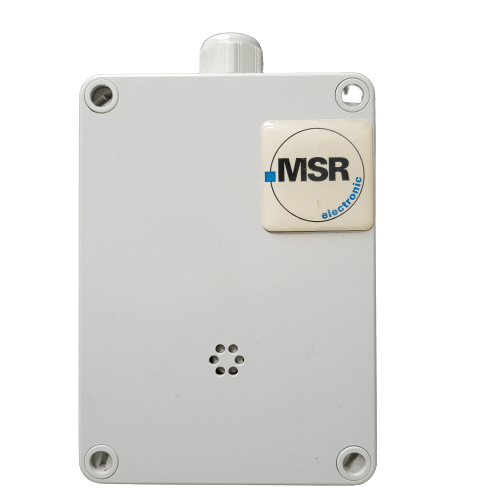
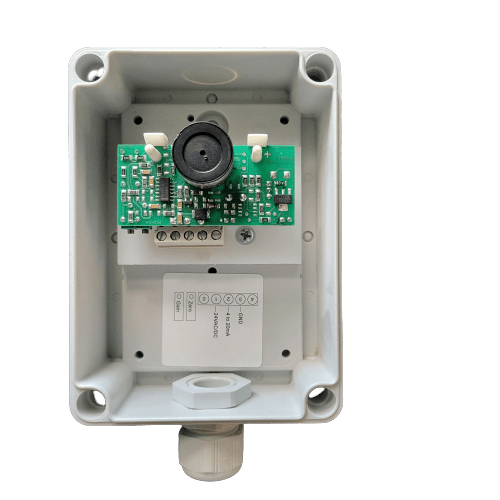
2007
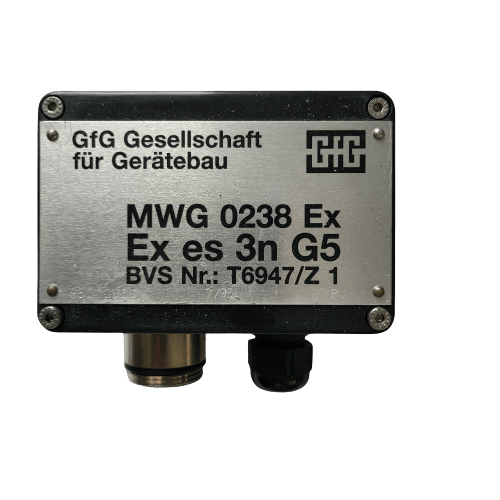
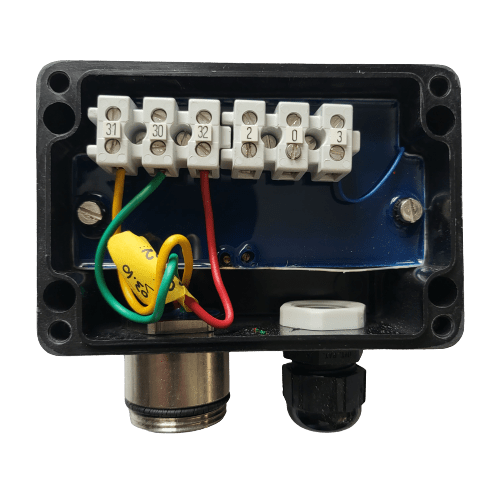
2008
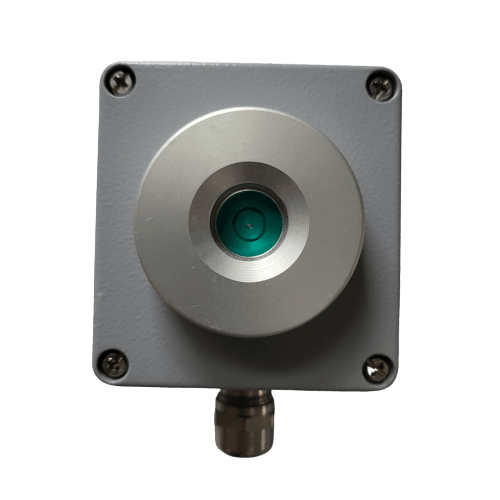
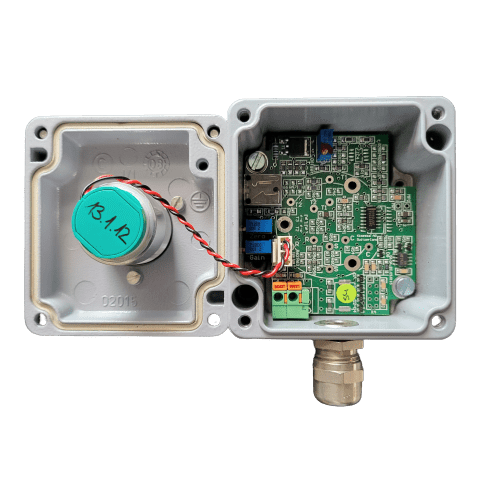
2009
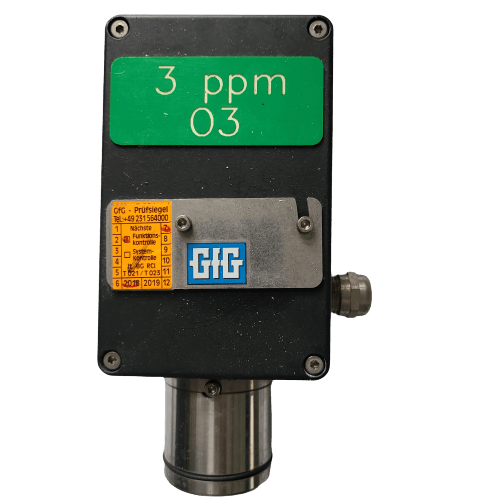
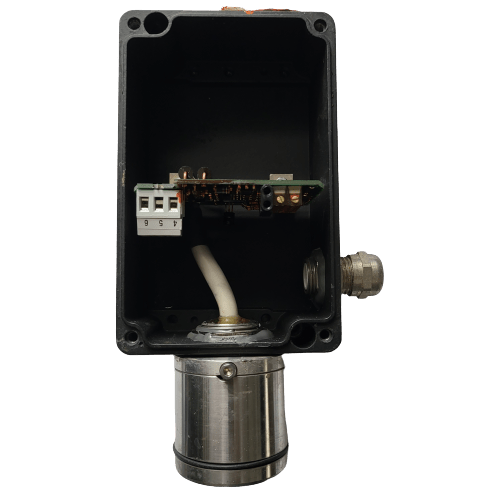
2010
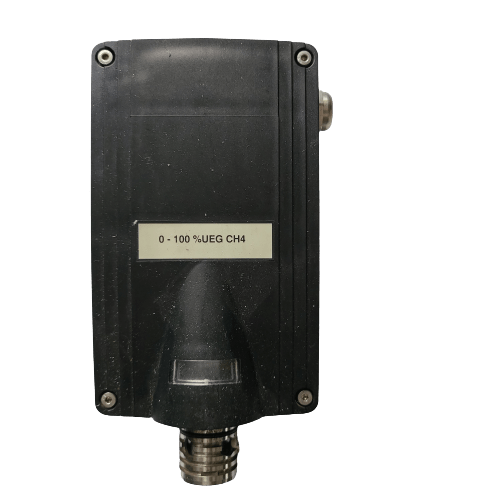
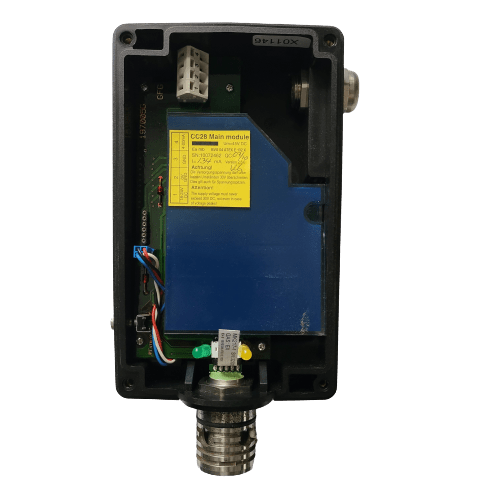
2013
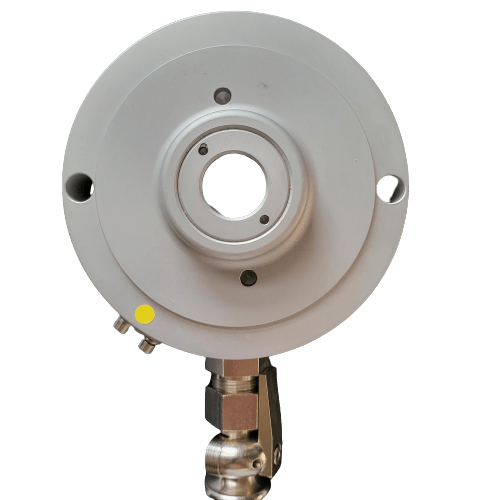
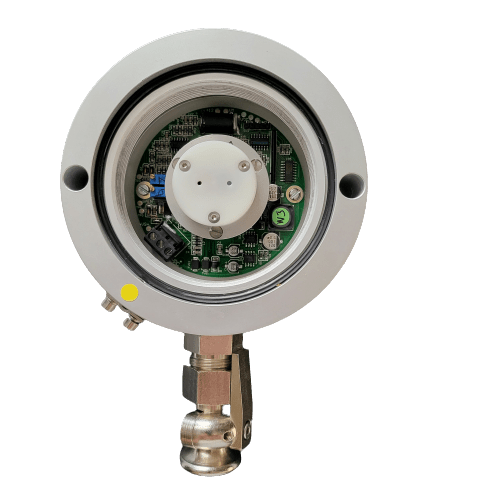
2015
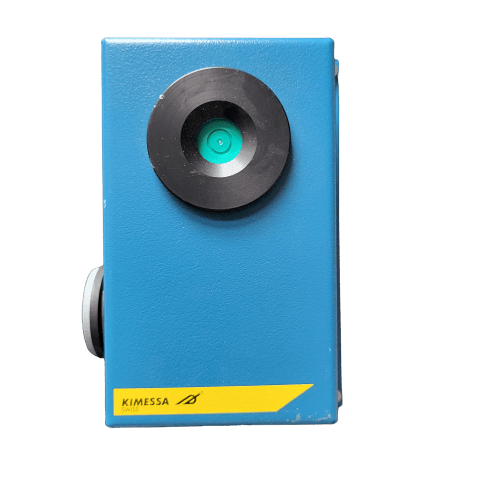
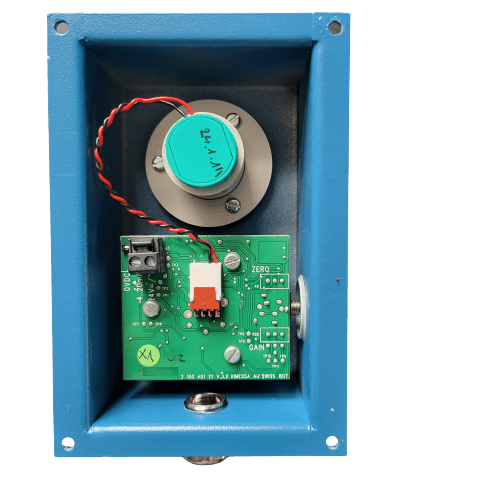
2016
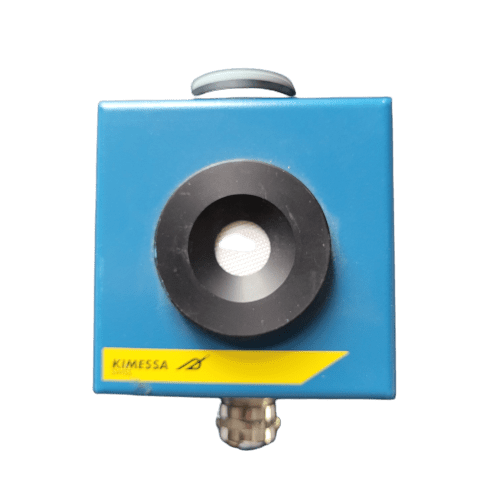
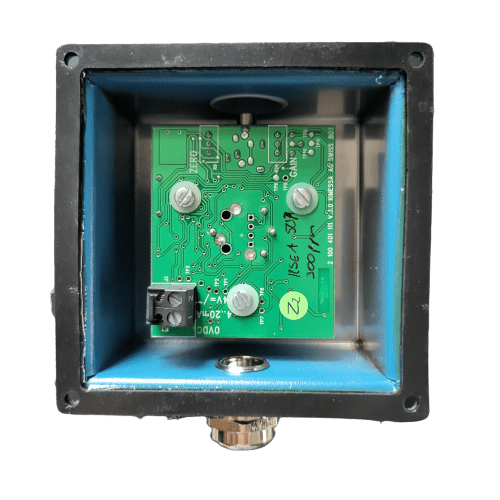
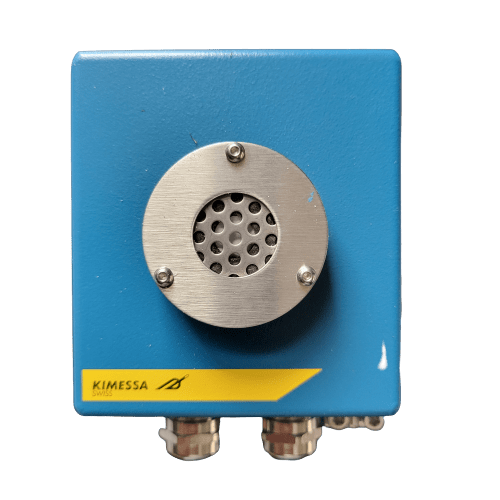
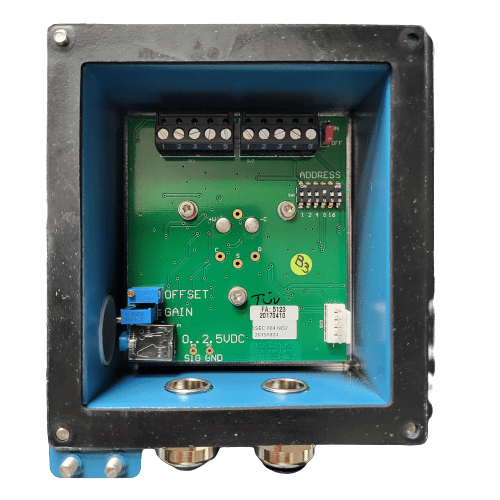
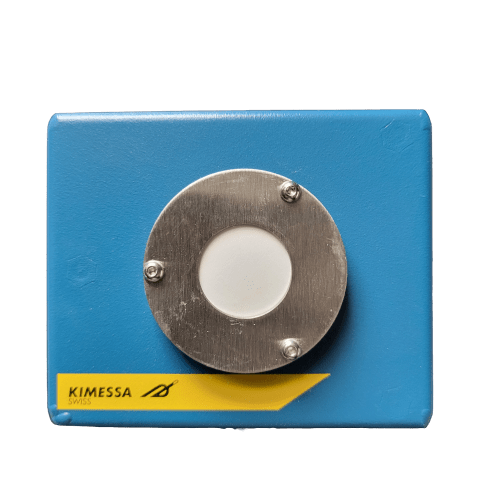
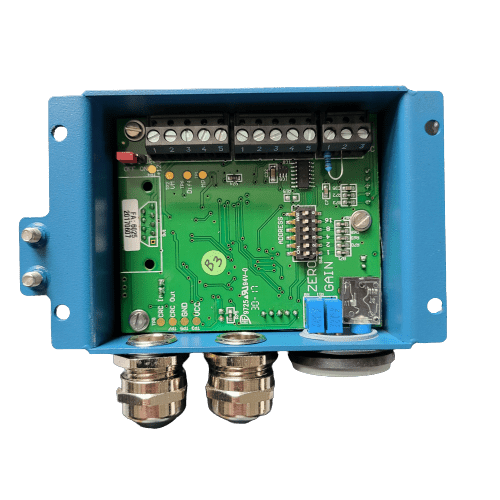
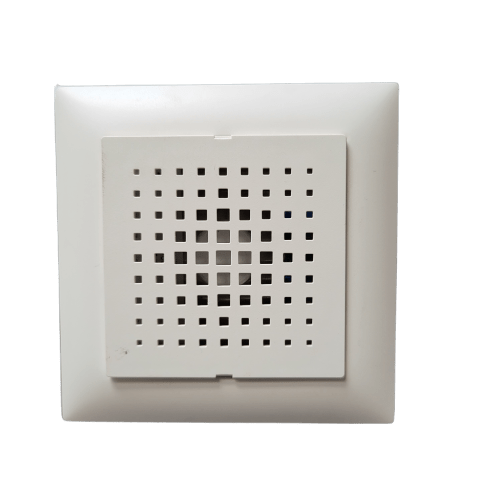
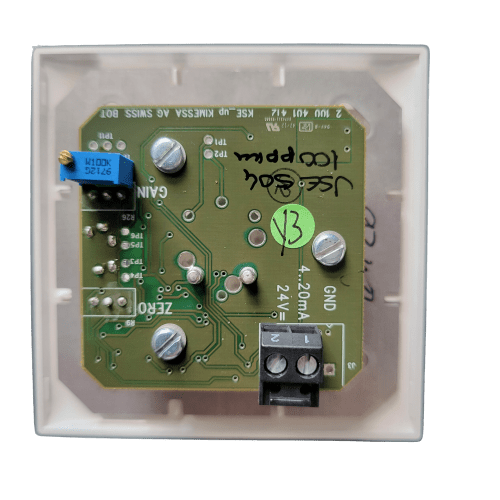
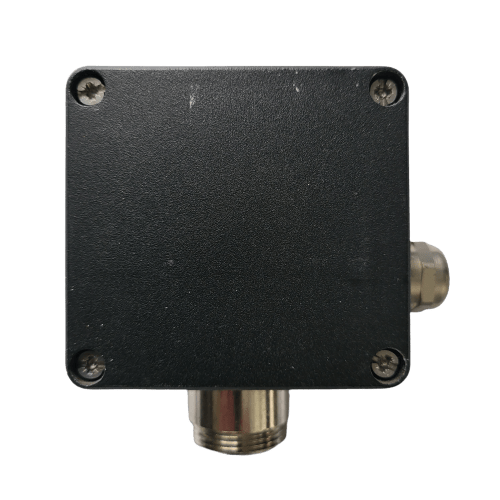
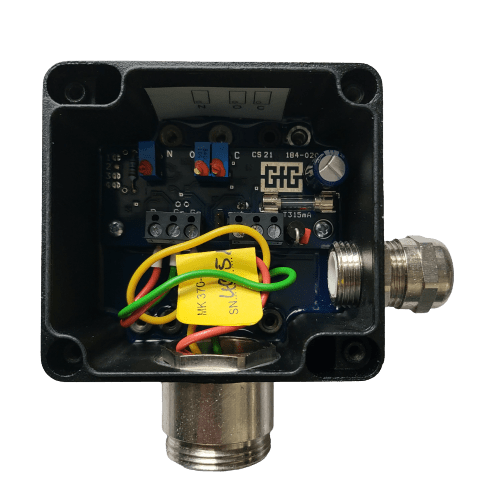
2017
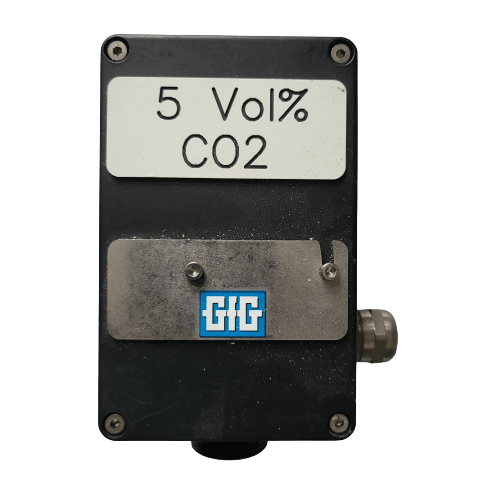
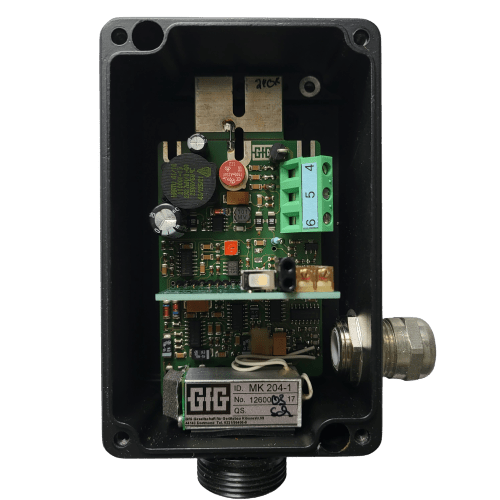
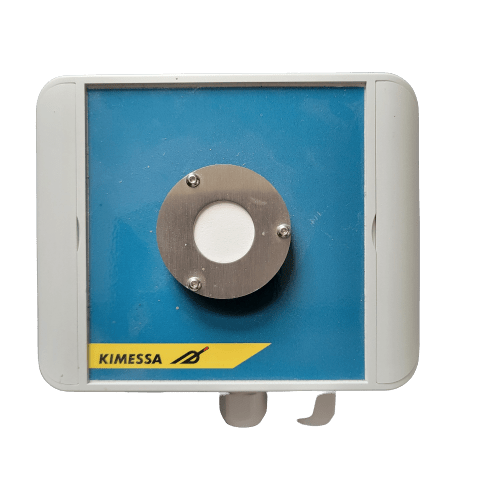
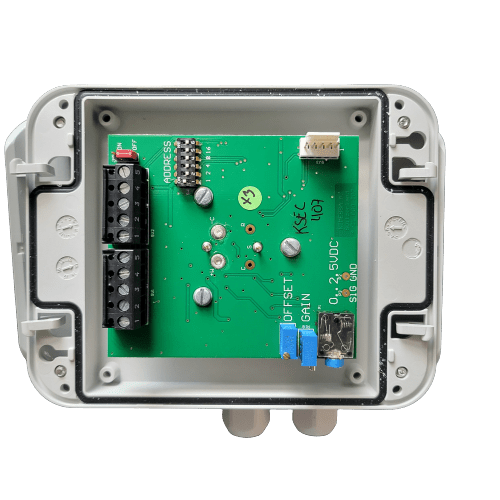
2018
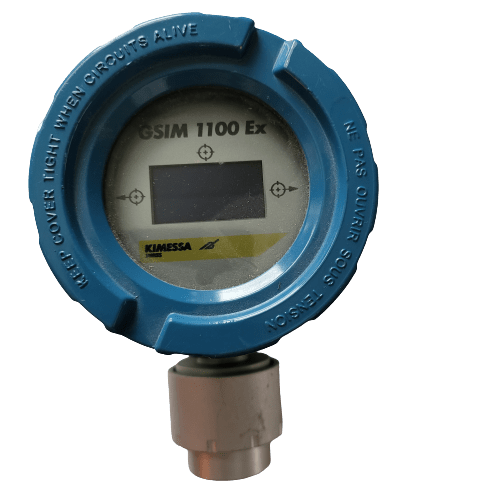
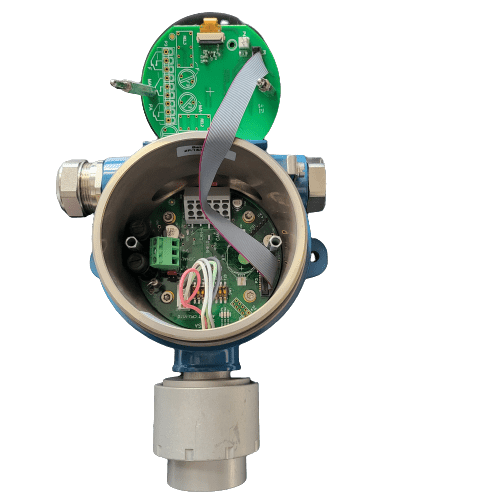
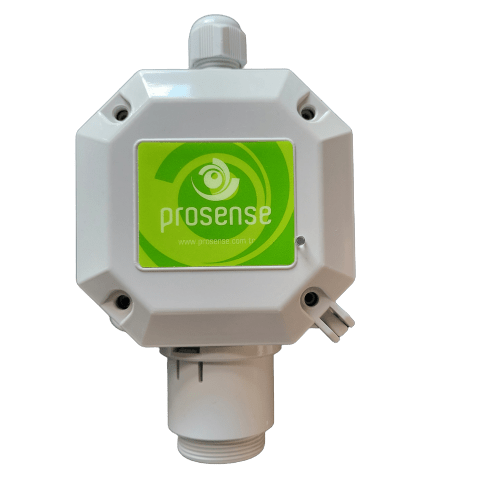
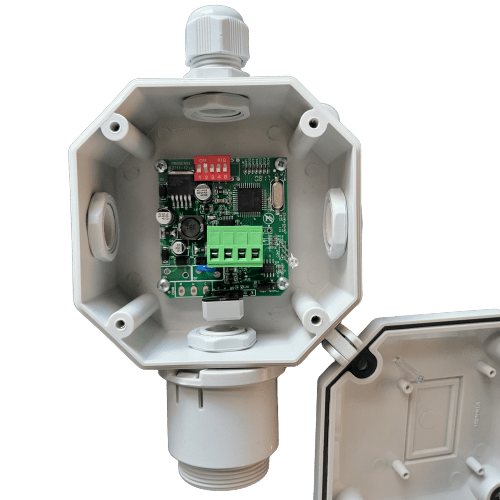
2019
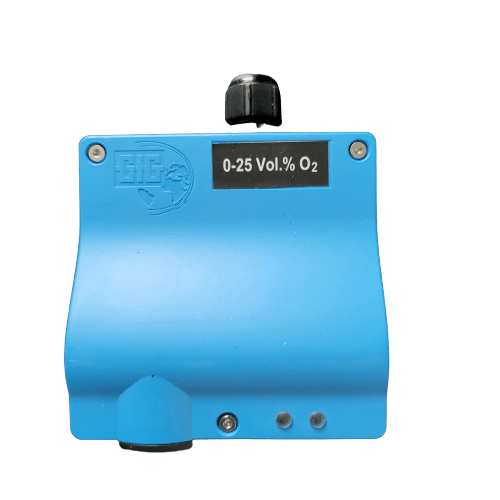
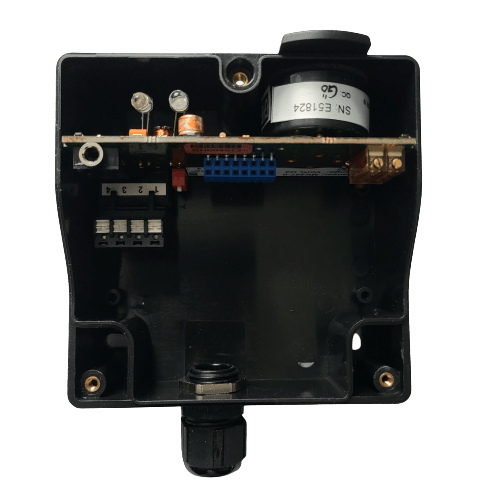
2020
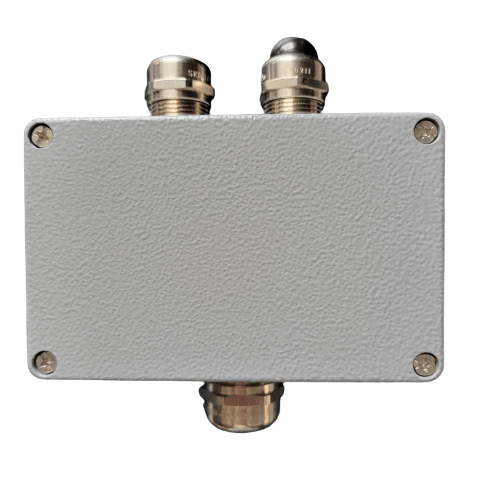
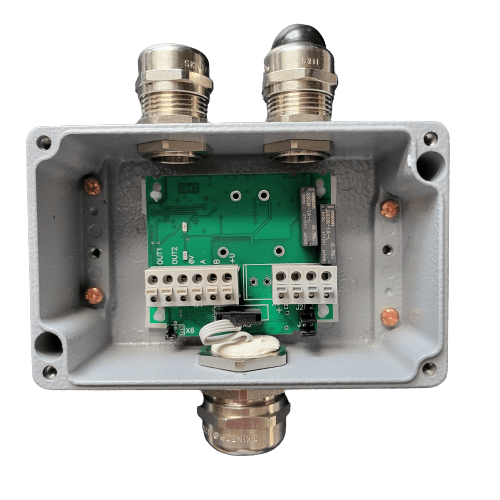
Tel. 06004 930 110
E-Mail